圆柱电池模块母线焊接
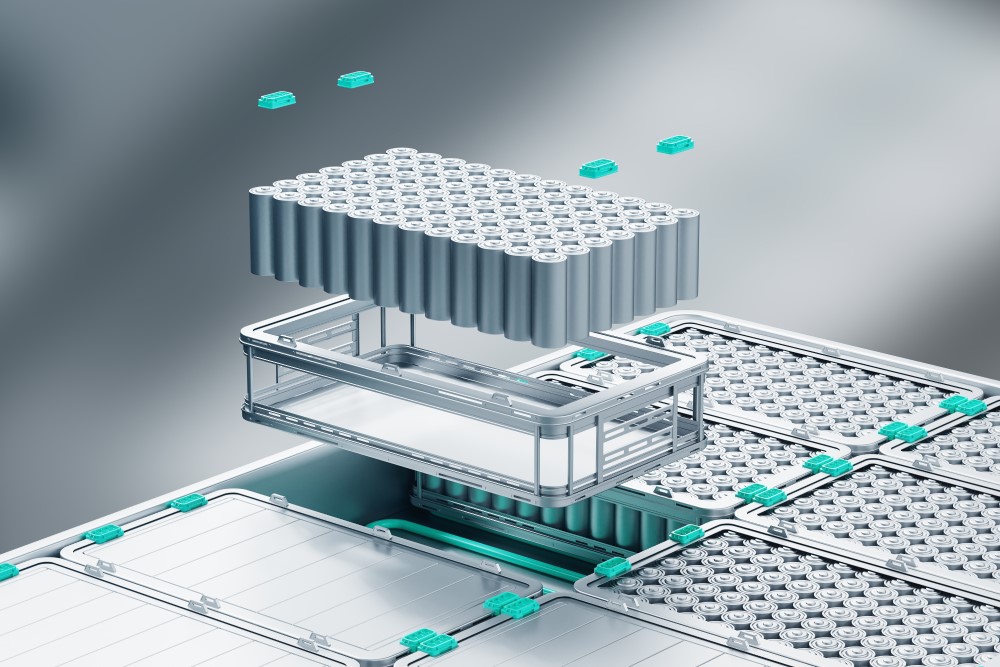
加热电池模块的母线焊接
在汽车应用中,许多单独的电池必须通过电气连接至母线才能驱动电动机。这个过程既耗时又昂贵,而且很难实现稳定的质量。K2 LASER SYSTEM 为圆柱电池模块提供母线精密焊接解决方案。激光器可以实现出色的自动化生产工艺,并且该过程具有很高的可重复性和可靠性。基于在汽车电池行业积累的多年专业知识,我们满足更高的质量要求。
集成监控系统
为了精确控制接头深度并防止焊接过程中出现质量问题,脉冲激光器、OCT 和视觉系统采用同轴配置。根据自动测量的母线距离和位置,对焊接位置进行三维精确校正,并对激光束进行定位。通过减少不必要的位置移动,可以减少物流系统中发生的机械错误,以及由于先进的加工而导致的单元高度偏差高达 1 mm。此外,由于测量、处理和检查的三步过程是同时进行的,因此可以实现更强的自动化连续生产。
更多工作区域
激光系统的加工区域是决定生产率的关键规格,我们的系统最大限度地减少了加工区域内的焦点偏转,并提供多达 4 X 4 个单元的宽加工区域,以实现更高的加工速度和生产率。由于激光模块的位置可以移动,因此可以根据机器人轴和舞台尺寸扩大整个加工区域。即使在这种情况下,随着长时间工作的持续,通过减少反复移动电池组所需的时间,也大大降低了整个系统的复杂性。
大面积细胞阵列批量焊接
从放入装有电池的模块到完成阳极和阴极之间的所有电气连接,批量工作都是进行的。当高分辨率视觉传感器自动校正加工位置时,脉冲激光器会高速进行局部粘合。具有最高自动化水平的批处理系统可降低因过程之间的转移而导致的缺陷率,并最大限度地减少批次间的偏差。
非接触式激光精密加工
电池对物理缺陷很敏感。在不接触材料的情况下进行精密加工。
- 防止材料因接触而变形和损坏
- 通过对数十个脉冲进行叠加处理,最大限度地减少了 HAZ
实时质量监控
通过实时检测焊接缺陷,可以在所有连接点实现完美的电气接合。
- 加工前/加工后自动对准
- 处理期间的处理中监控
灵活的处理设计
工作流程和参数可以根据单元和模块的设计和布局进行调整。
- 用于加工和监控的集成结构设计
- 自动探索扩展的工作空间
全自动系统
该自动化系统以最短的循环时间快速处理数百个接头。
- 位置搜索、处理和检查的综合流程
- 针对材料和工艺进行了优化的工艺配方
提高了质量和生产力
连续波光纤激光器持续发射能量,焦距非常小,仅为 30 um,并且需要 300 W 或以上的高热输入。由铝和钢制成的异质薄板,例如模块母线,表现出敏感的热响应,这通常会导致焊接不力和贯穿焊接等缺陷。
我们的高精度 ns 脉冲激光器通过增加激光器的峰值输出来减少热量输入。与简单的点焊不同,数十个脉冲以高频率紧密叠加,从而减少了金属间化合物(金属间化合物)的出现并实现了优异的异质粘合。
Conclusion
我们的母线焊接解决方案是针对圆柱形电池和模块进行了优化的自动化系统。使用紧凑型风冷激光器实现的激光系统可以以经济的成本实现卓越的生产率和可用性。特别是,当与智能监控头结合使用时,可以实时读取焊接缺陷和变形,以保持最高的质量水平。
- 最大处理面积:90 x 90 mm,4 x 4 个电池
- 处理速度:高达每秒 10 个以上的单元
- 夹具设计针对电池模块设计进行了优化