Cylindrical battery module busbar welding
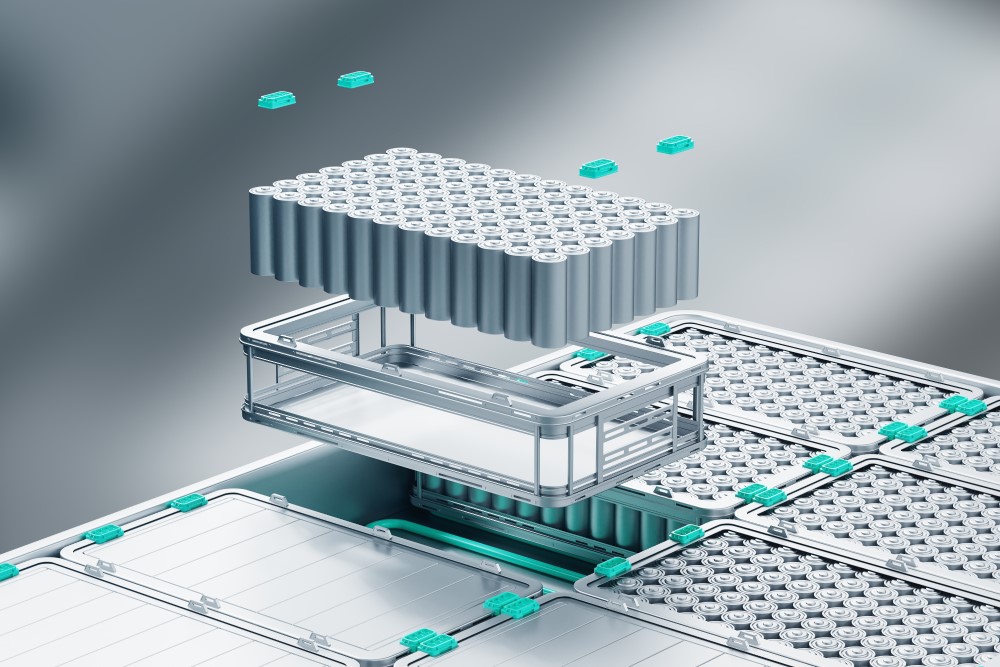
Busbar welding for heating battery module
In automotive applications, many individual batteries must be electrically connected to a bus bar to drive an electric motor. This process is time-consuming and expensive, and achieving consistent quality is difficult. K2 LASER SYSTEM provides a busbar precision welding solution for cylindrical battery modules. Lasers can implement excellent automated production processes with high repeatability and reliability of the process. We satisfy increased quality requirements based on years of know-how accumulated in the mobility battery industry.
Integrated monitoring system
In order to precisely control the depth of the joint and prevent quality problems that occur during the welding process, a pulse laser, OCT, and vision system are coaxially configured. The welding position is accurately corrected in three dimensions according to the automatically measured distance and position of the bus bar, and the laser beam is positioned. By reducing unnecessary position movement, it is possible to reduce the occurrence of mechanical errors in logistics systems and cell height deviations of up to 1 mm due to advanced processing. Furthermore, since the three-step process of measurement, processing, and inspection is carried out at once, more enhanced automated continuous production is possible.
More work area
The processing area of a laser system is a key specification that determines productivity, and our system minimizes focus deflection within the processing area and provides a wide processing area of up to 4 X 4 cells to achieve even higher processing speed and productivity. Since the position of the laser module can be moved, the entire processing area can be expanded according to the robot axis and stage size. Even in this case, the complexity of the entire system is greatly reduced by reducing the time required to move the battery pack repeatedly as the extended work lasts.
Large area cell array batch welding
Batch work is carried out from putting in a module equipped with a battery cell to completing all electrical connections between the anode and cathode. When the processing position is automatically corrected by a high-resolution vision sensor, pulsed lasers perform local area bonding at a high speed. A batch system with a maximum level of automation reduces the defect rate due to transfer between processes and minimizes lot-to-lot deviations.
Non-contact laser precision machining
Battery cells are sensitive to physical defects. Precision machining is performed without material contact.
- Preventing material deformation and damage due to contact
- HAZ minimized by superimposition processing of dozens of pulses
Real-time quality monitoring
By detecting welding defects in real time, perfect electrical bonding is achieved at all connection points.
- Auto Alignment Before/After Machining
- On-processing monitoring during processing
Flexible processing design
Work processes and parameters can be adjusted according to cell and module design and layout.
- Integrated structure design for machining and monitoring
- Automatic exploration of extended workspaces
Fully automated system
The automated system quickly processes hundreds of joints with minimal cycle time.
- Integrated process of location search, processing, and inspection
- Process recipes optimized for materials and processes
Improved quality and productivity
CW fiber lasers emit energy continuously, and the focal size is very small at the level of 30 um, and a high heat input of 300 W or more is required. Heterogeneous thin plates made of aluminum and steel, such as module bus bars, show a sensitive thermal response, and this frequently causes defects such as weak welding and through welding.
Our high-precision ns pulse laser reduces heat input by increasing the laser's peak output. Unlike simple spot welding, dozens of pulses are tightly superimposed at a high frequency, which reduces the occurrence of intermetallic compounds (Intermetallic Compounds) and enables excellent heterogeneous bonding.
Conclusion
Our busbar welding solution is an automated system optimized for cylindrical battery cells and modules. Laser systems implemented with compact, air-cooled lasers can achieve excellent productivity and availability at an economical cost. In particular, when combined with a smart monitoring head, weld defects and deformation can be read in real time to maintain the highest level of quality.
- Maximum processing area: 90 x 90 mm, 4 x 4 cells
- Processing speed: up to 10+ cells per second
- Clamping jig design optimized for cell module design