About Industrial laser welding machines
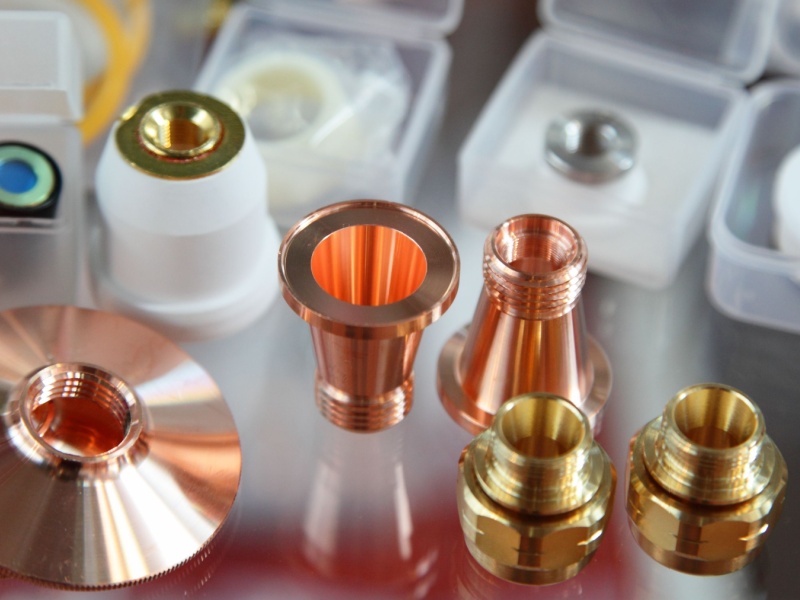
TL; DR:
- What is an industrial laser welding machine Secondary batteryIt is widely used in various industries such as electric motors, and provides precise welding.
- Laser welding uses a laser beam for metals and thermoplastics plasticsIt is a welding technology that joins.
- The advantages of laser welding include precision, minimal heat input, high weld quality, versatility, speed, and efficiency.
- The disadvantages of laser welding include equipment costs, high technical requirements, limited joint thickness, and sensitivity to surface conditions.
- Blue laser, multi-beam laser, and multi-focus laser welding technology are evolving with the latest trends.
Industrial laser welding machines are an ideal technology for precise welding work, and are used in various industries such as automotive, aerospace, and medical device manufacturing. In this blog post, we'll take a detailed look at the technology, processes, equipment, and considerations of industrial laser welding machines.
The definition and working principle of an industrial laser welding machine
Laser welding is a welding technology used to join pieces of metal and thermoplastic using a laser beam. This method is a method of heating and melting the welding area with a laser beam, which is suitable for narrow or deep welds and extremely fast welding. Laser welding is compatible with a wide range of materials and provides precise connections. Also, the process of welding using a laser welding machine is a method of melting and connecting workpieces using laser energy. Laser welding is possible because the energy of the laser is very high, but more accurate, the energy density is very high because the laser energy is extremely high at one point. Based on this principle, laser welding is being used in various industries.
Laser welding provides precise work and fast welding speed, and is frequently used in the automotive industry, jewellery, metal processing, etc. Also, since laser welding uses a laser, it has the great advantage of not surprising other areas. Laser welding is classified into various types according to the regulations of the laser beam. Thermal conduction welding is a method in which the material conductive melts in the surface layer due to the low output density of the laser beam and the long laser irradiation time. In comparison, keyhole welding removes a deeper, narrower weld, and the molten material fills the keyhole to form a weld bead. Laser welding is using various laser types, including solid-state lasers, gas lasers, and fiber lasers. Laser welding is a precise welding technology using a laser beam, and is used in various industries.
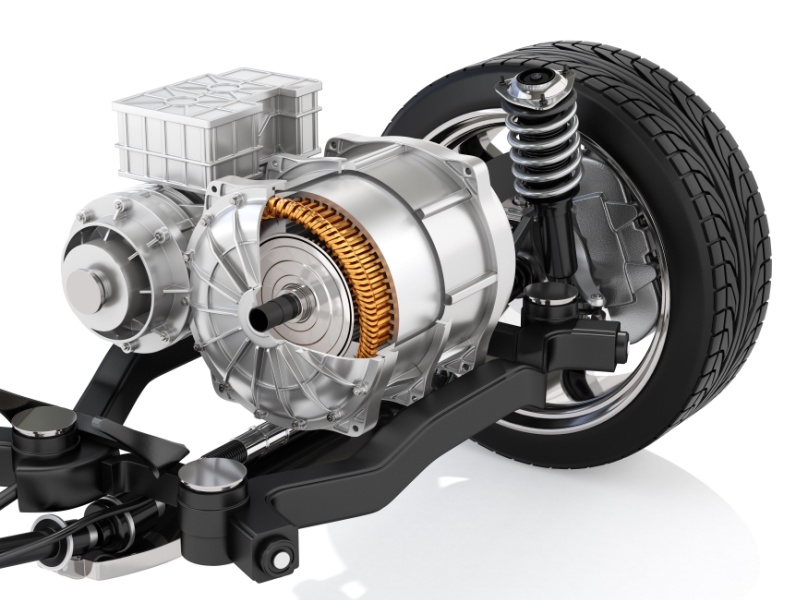
Pros and cons of laser welding machines
Laser welding is a modern and efficient method of joining materials in various industries, and has several advantages and advantages. Let's take a look at the major pros and cons of laser welding below.
Advantages of laser welding
- Precision and control: Laser welding can reduce control welding parameters, accurate and repeatable welding even with complex shapes.
- Minimal column input: Combining to traditional welding methods, laser welding reducing minimal heat to the material, reducing the risk of warping and thermal damage in difficult areas.
- High weld quality: Laser welding minimizes and provides excellent weld strength and minimal potential for holes and defects due to the small heat-affected zone.
- versatility: Can work on a wide range of materials including metals, plastics, ceramic, and dissimilar materials.
- Speed and efficiency: Laser welding is a challenging process, reducing productivity and reducing manufacturing costs.
- Non-contact process: Laser welding is a non-contact process that requires operating costs by not consumable electrodes or fillers.
- Minimal post-weld finish: Laser welding can reduce post-processing work by pleasing and aesthetically pleasing welds.
- Automate and integrate: Laser welding is highly compatible with automation systems and can be integrated into production lines.
Disadvantage of laser welding
- Equipment costs: Can laser welding equipment have high initial investment and maintenance costs
- High technical requirements: Professional training and expertise are required to operate a laser welding system
- Limited joint thickness: Laser Welded May Have Fabrications for Thick Joints
- Sensitivity to surface conditions: Laser welding requires a clean and well-prepared surface to achieve optimal weld quality
Laser welding is a preferred process in many industries due to its benefits, but it's important to reduce the associated costs, technical requirements, and benefits. As technology advances to advance, laser welding is expected to further advance, introduces more opportunities to enhance manufacturing processes and product development.
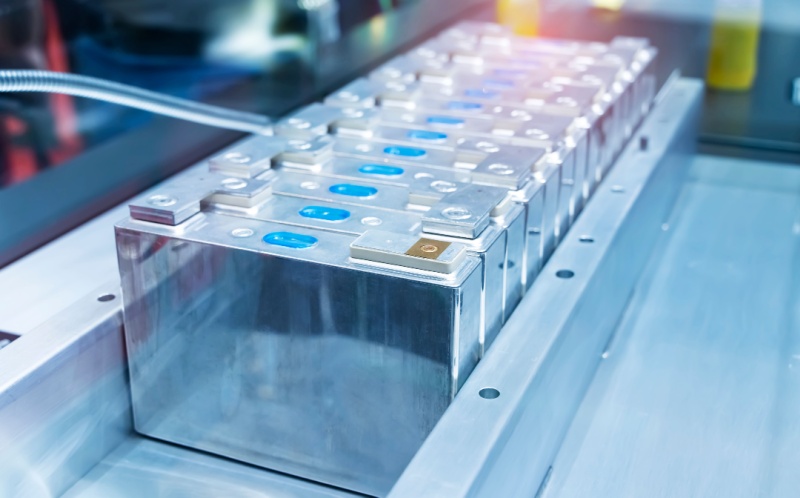
Laser welding technology trends
Laser welding technology continues to advance and is being used in various fields. Below, we'll look at the latest trends and development directions in blue laser, multi-beam, and multi-focus laser welding technology.
Blue laser
Blue lasers are high-energy lasers with a wavelength of approximately 450 nm. Compared to fiber lasers, it has a higher absorption rate for metals such as copper, nickel, titanium, aluminum, steel, brass, and gold.
Main applications:
- E-Mobility Hairpin: Used for welding hairpin motors in electric vehicles. The hairpin motor uses copper, and laser welding provides uniform weld quality.
- Battery cell: Laser welding is applied to the terminal connection of the battery cell. In particular, laser welding is used as a way to increase the number of battery terminals.
- Battery case: Laser is applied to lithium ion battery case welding to prevent foreign matter from penetrating into the interior and improve welding quality.
Multi-beam lasers
Multi-beam lasers are a technology that combines and welds multiple laser beams. The use of multiple beams increases welding speed and efficiency.
Main applications:
- Car manufacturing: Used for welding various parts such as car bodies, engine parts, and exhaust systems.
- Aviation and space industry: Suitable for welding aircraft parts, spacecraft structures, rocket engines, etc.
Multi-focus
Multi-focus lasers perform precise welding by having a DOF extended to multiple focal points without mechanical focal length adjustment. It is a welding technology suitable for small parts and complex structures. It provides a fast work speed and is popular in manufacturing industries looking for high productivity.