Laser notching machines for battery electrodes: essential solutions to increase productivity and efficiency
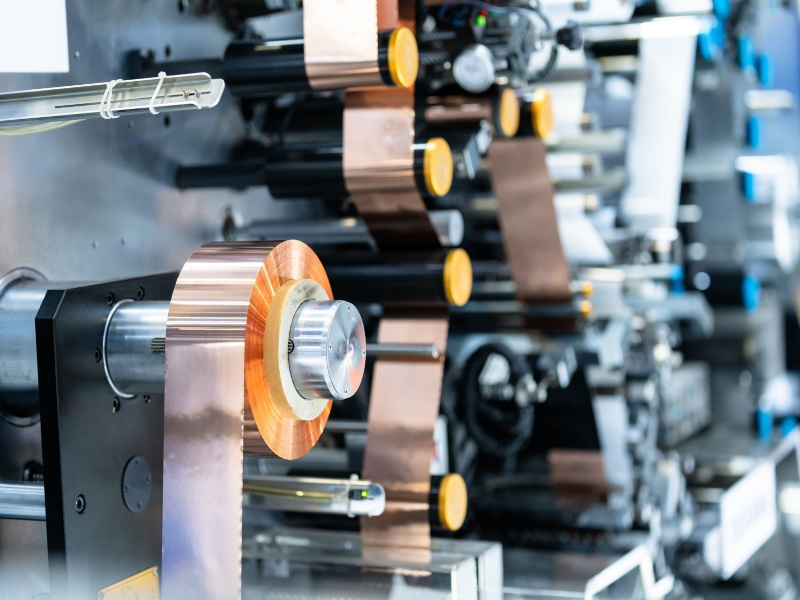
What is laser notching technology?
Laser roll-to-roll notching equipment is a key equipment used in the secondary battery manufacturing process. This equipment uses a laser to perform the process of cutting the core battery material of a secondary battery into a tab with the correct length and shape. Compared to traditional mold cutting methods, laser notching has a faster cutting speed and reduces heat loss during processing. In addition, laser notching equipment can precisely cut electrode materials by irradiating a laser source in nanoseconds, and this is a technology that cuts a laser light source by shooting a laser light source for a very short period of time, which means 1/1 trillion seconds
This equipment contributes to improving electrode quality and yield by finely cutting anode and cathode materials to a fixed size. The introduction of laser notching equipment is attracting attention due to its advantages such as reducing battery manufacturing time and costs, reducing defect rates, and improving production speed.
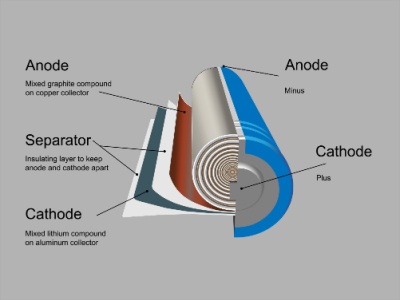
5 amazing benefits of laser notching systems
Laser notching systems have a number of remarkable advantages over traditional mold cutting methods. Here are five of its key benefits:
- Yield improvement: Laser notching can cut the anode and cathode tabs more cleanly, reducing breakage that occurs when the cut surface is not cut evenly and remains uneven
- cost efficiency: Laser notching solves the problem that the press blade replacement cycle is once every 3 days, and the process efficiency is reduced by 30% compared to the traditional method of shutting down the entire line. Also, there is a high press blade replacement cost per line per month, which can be reduced
- Increased productivity: Laser notching can be designed in multiple layers, which can greatly improve the yield per unit area. Conventional presses are impact-intensive, making it impossible to design two layers, while laser notching makes this possible
- Labor cost reduction: Replacing existing press blades requires manpower, but laser notching can reduce these labor costs
- Reduced cutting speed and debris generation: Compared to conventional press notching, laser notching has the advantage of faster cutting speed and less foreign matter. The initial setup is expensive, but the maintenance costs are low, making it economical in the long run
The structure of an excellent laser notching system
Laser notching equipment equipped with a high-speed scanner is a key equipment for precise cutting of anode or cathode materials in the secondary battery manufacturing process. This equipment uses a laser to accurately adjust the length of the electrode material and form the required notch.
- laser source: The laser notching equipment uses a fiber laser source. Fiber lasers provide high energy efficiency and reduced carbon emissions, and are effective in lithium-ion battery production.
- high speed scanner: The laser notching equipment is equipped with a high-speed scanner. This scanner precisely manipulates the laser beam to quickly cut the electrode material. The high-speed scanner controls the speed and direction of movement of the laser beam, and performs the function of finding a new cutting line in real time.
- vision system: Laser notching detects the position of the electrode material in real time through a vision system. The system calculates the compensation position so that the laser beam performs cutting at the correct position, and automatically finds a new cutting line even if the material is wrong.
Conclusion: Open up the future of battery production with laser notching machines
It can be said that the technical prospects for laser notching equipment using roll-to-roll systems are very bright. Looking at recent research and market trends, this technology plays a particularly important role in the secondary battery manufacturing process, and various domestic and international companies continue to develop related technologies and make efforts to improve efficiency. This technology is far more precise and productive than conventional mechanical notching methods. It is very effective for mass production, especially when applied to roll-to-roll processes. Laser notching systems using galvano scanners can produce consistent electrode quality with fast scan speed and accurate position control.