laser equipment for secondary batteries
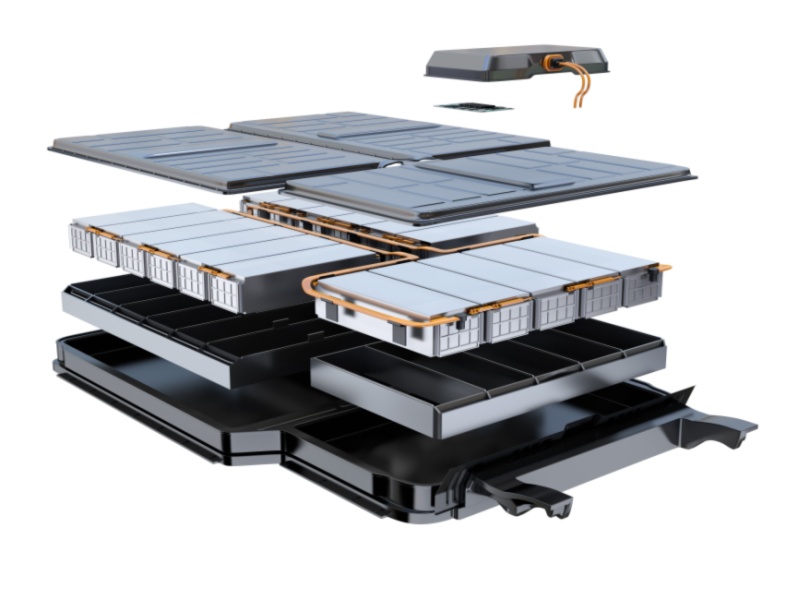
The main processes in which lasers are used in secondary battery manufacturing are 1. Electrode process, 2. Assembly process, 3. There is a module pack process. Before explaining the details of each process, this article will discuss the main types of laser processes.
1. Electrode process
A process for making anodes and cathodes by mixing active materials, conductive materials, and binders that make up an electrode after putting in raw materials.
- Drying: Electrodes coated with active material will go through a drying process after coating. Lasers are more energy efficient and have a smaller footprint than traditional hot air drying. Also, since only the dry layer is intensively processed, work time is shortened.
- Structuring: The surface of the coated electrode is structured in various shapes to improve energy density and battery performance. The increased surface area increases the diffusion path of lithium ions, which not only increases output, but also reduces mechanical stress due to volume expansion of the electrode material, contributing to improved battery stability. It is important to optimize laser processing conditions and shapes according to the characteristics of the material.
2. Assembly process
The process of stacking plates transferred from the electrode process, putting on a cap or sealing a pouch, and injecting electrolyte solution.
- Notching: The electrode that has completed the slitting process is inserted into the notching process along the roll. To assemble according to the cell shape, the anode and cathode tabs are machined on the electrode foil. Uncoated plain parts must be precisely machined to the correct length and shape. The press method requires periodic replacement due to blade wear, and there is a limit to improving the quality of the electrode due to dirt generated during cutting. In contrast, lasers minimize material deformation with minimal HAZ and non-contact processing.
- Tap welding: In order to collect the current flowing from a single plate in one place, aluminum and copper tabs are welded to the blank parts of the anode and cathode of the stacked battery, respectively. Previously, tabs were bonded using ultrasonic waves with heat caused by vibration at the joint, but there were restrictions on shape and space. Lasers, on the other hand, can achieve excellent heterogeneous metal-to-metal bonding because they use a very small beam of high energy density.
- Packaging: A process in which cells are sealed according to each format after injecting an electrolyte solution. For square and cylindrical shapes, an aluminum metal case and can (CAN) are housings, and the upper part closed by a cap (Cap) is laser-welded. Pouch-type batteries are packaged using an aluminum film pouch with a multi-layer structure as the housing and heat is applied. Laser sealing of pouch-type batteries is also being considered as internal configuration complexity increases.
3. Module pack process
Modules and packs are manufactured by integrating individual battery cells.
- Busbar welding: Busbars are welded to electrically connect multiple cells in series. Generally, a thin aluminum bus bar or plate is superimposed and welded onto a thick copper bar. The laser performs precise full penetration welding without damaging thin aluminum foils. It is important to prevent damage to cells and peripherals through process optimization that minimizes the occurrence of spatter.
- Housing welding: the battery module is joined to the battery box For weight reduction, 5xxx and 6xxx series high-strength aluminum alloys are mainly used. It is important to suppress cracks and spatter caused by pores and high temperatures in the alloy itself. It is important to select the optimal laser according to the characteristics of the material and maintain a uniform energy distribution.