Plastic lamp simultaneous inspection welding
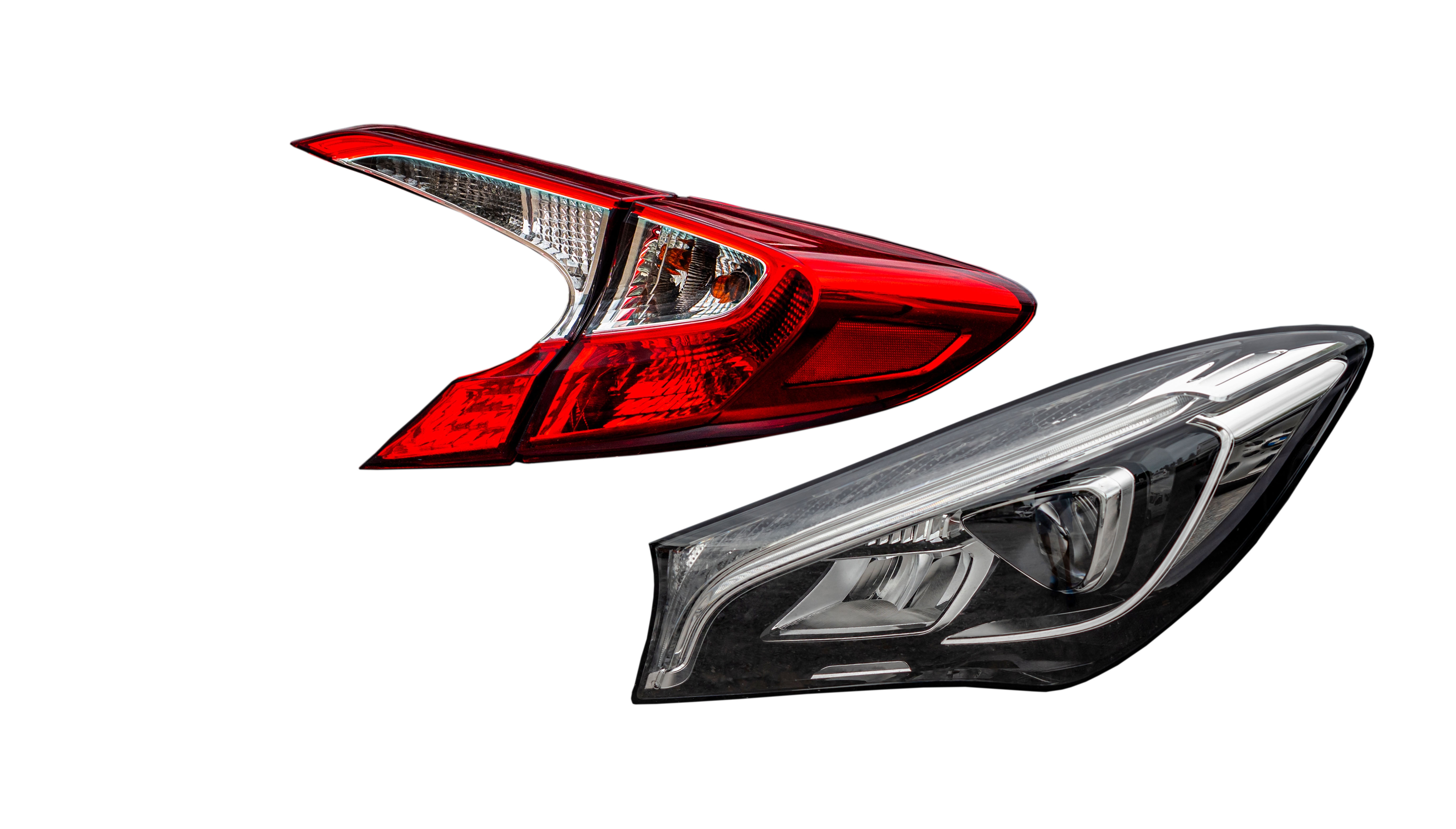
Welded plastic transmission welding
If the lamp has a wide joint, sufficient adhesiveness can also be secured by a fusion method using vibration and heat. However, vibration welding has limitations on the direction of vibration and pressure, so products with large curvature have limitations. Laser transmission welding can join all materials transmitted by the laser's wavelength without being visually “transparent”. K2 achieves excellent processing quality with the simultaneous survey method, which is an advanced transmission welding method.
The most optimized transmission method
Laser plastic welding technology, which provides excellent joint quality without the use of adhesives, is showing higher reliability than ultrasonic or vibration welding in various industries. Laser technology has the advantage of being able to effectively protect sensitive electronic components by concentrating thermal energy locally. A laser with a unique wavelength penetrates the permeable plastic and heats the absorbent plastic underneath. The heated material is bonded to the permeable layer which is bonded at the same time as melting. For permanent bonding, a weld seam equal to the stiffness of the material is created after maintaining the compression state for a certain period of time even after the laser irradiation is over.
1. Trajectory processing joint
Move the laser focus beam along the contour. The width of the connected lines can be adjusted by the size of the beam, which is more suitable for planar joints rather than curved shapes.
2. Hybrid trajectory machining
Halogen lamps support laser welding by emitting high heat. This preheats the processing line at the top, makes bonding smoother, and reduces deformation due to rapid heating.
3. Similar simultaneous processing
It combines contouring and simultaneous investigation methods, and moves the machining path several times at a very high speed. Overall, they are bonded almost simultaneously, and a uniform temperature distribution is maintained.
4. Simultaneous survey processing
The entire weld line is processed simultaneously. Joining in all areas is performed simultaneously with multiple fixed light sources, depending on the processing design, without moving the position of the laser beam.
The excellence of concurrent research
Vibration welding causes burrs and motion in the joint due to the gap between the jig and the injection rib. Furthermore, due to poor clamping operation, scratches occur on the exterior of the lamp lens, which reduces marketability. Simultaneous mold-integrated laser inspection is a method that can satisfy both fast execution and marketability.
Lamps must always maintain their watertightness despite various external changes faced during operation. K2 minimizes gaps in the laser irradiated area through mold-integrated pressurization. Also, without delay, all lamp welding surfaces are inspected simultaneously to block the source of motion.
The simultaneous survey method has a very high welding speed compared to traditional methods as well as conventional laser methods that weld along a line. Also, since the entire weld can be directly investigated simultaneously, condensation due to time differences is minimized and bonding strength is increased.
Productivity and quality you can trust
Laser transmission welding using the simultaneous irradiation method makes it very easy to control welding quality because the entire welding area is melted simultaneously, and the pressure or gap between the products to be welded is fixed. Also, since the processing time is very short compared to other methods, its superiority becomes clear when processing parts with high production volume and complex structures.
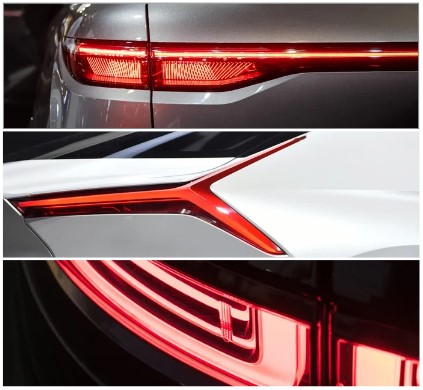
Conclusion
As a company specializing in laser optical solutions, K2 Laser Systems is developing an automated system incorporating Laser - Vision - Sensor's Coaxial Architecture. The transmissive simultaneous irradiation welding system is designed to fully meet the quality levels required for mobility components such as transparent sensors and lighting lamps.
K2 Laser's simultaneous irradiation system is designed with a structure that enables uniform melt pool formation and rapid bonding. Based on accumulated experience in the mobility industry, designs that are faithful to customer requirements are reflected, from diode lasers to bundles and waveguide bonding methods.
Waveguide integrated clamping jig
- Maximizing the level of automation in process systems
- Online quality monitoring and feedback
- Flexible process design and easy implementation
Efficient and clean work
- Zero particles with non-contact three-dimensional fusion
- Processes without structural modifications and consumables
- Flexible process design and easy implementation