Airbag Scoring
Airbags are the last bastion for protecting lives in the event of a vehicle accident. It does not respond to shocks absorbed during the vehicle's daily driving, but if it can cause injury, the CRASH PAD must be torn apart to protect the occupants. To increase the reliability of safety devices, all structures must operate in an analog manner, and LASER SCORING enables higher quality and more flexible work compared to physical methods using knives.
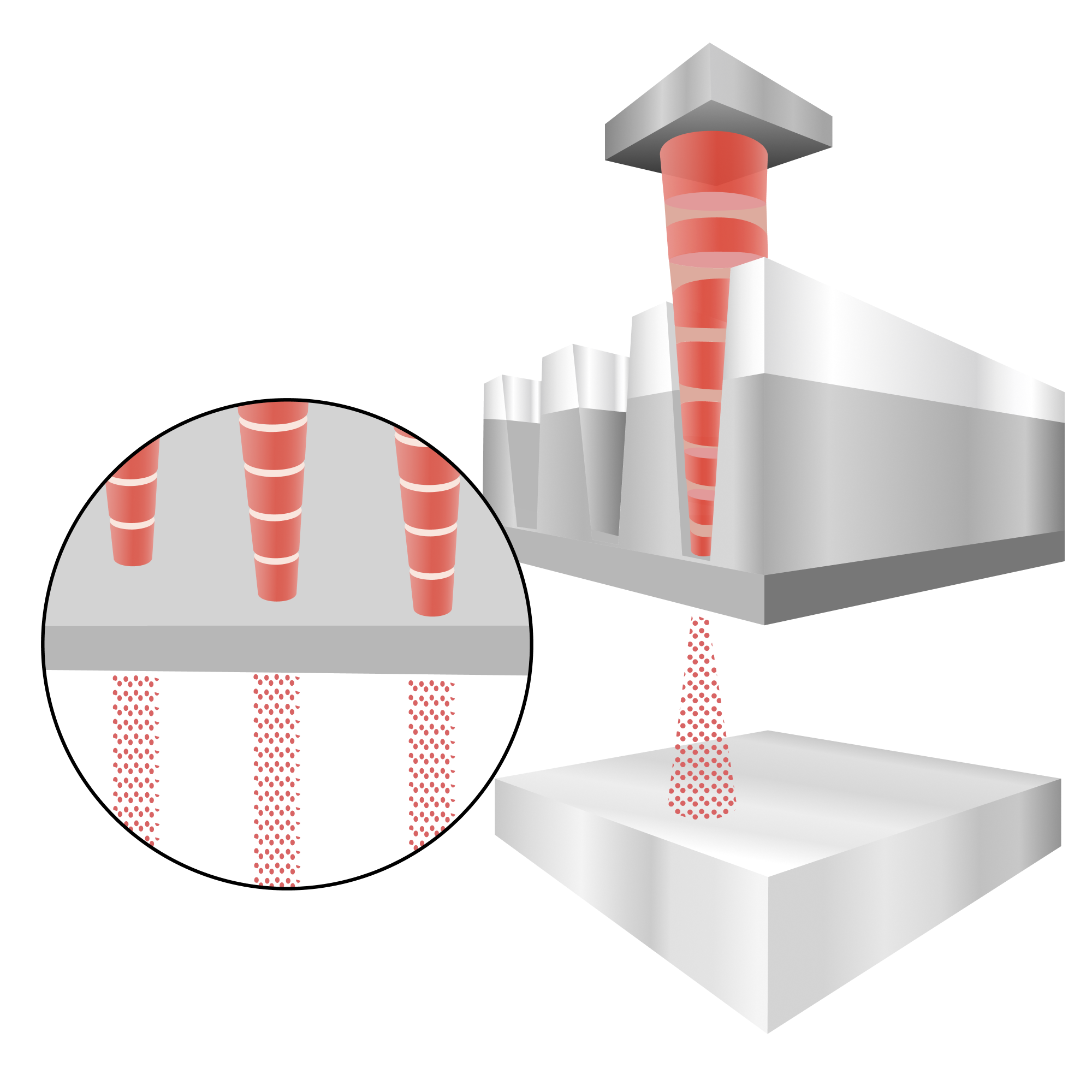
Features
LASER BEAM
A sensor mounted on the laser emitter is used to improve the accuracy of reading and feedback on the processing position. After the beam is incident, the output is automatically controlled through processing depth and remaining amount data measured by the light sensor.
Substrate
With the exception of the skin, crash pads are composed of plastic-based materials, and the built-in materials laminated in multiple layers are also from different manufacturers. Using a CO2 laser, processing can be performed regardless of the material.
FOAM
By processing using a laser, crash pads made of multi-layer materials can be processed in a single process. Not only is process time dramatically reduced, dust generated by processing is suppressed to a low level, and residue is effectively removed.
LASER BEAM
A sensor mounted on the laser emitter is used to improve the accuracy of reading and feedback on the processing position. After the beam is incident, the output is automatically controlled through processing depth and remaining amount data measured by the light sensor.
Substrate
With the exception of the skin, crash pads are composed of plastic-based materials, and the built-in materials laminated in multiple layers are also from different manufacturers. Using a CO2 laser, processing can be performed regardless of the material.
FOAM
By processing using a laser, crash pads made of multi-layer materials can be processed in a single process. Not only is process time dramatically reduced, dust generated by processing is suppressed to a low level, and residue is effectively removed.
FOIL/SKIN
Although internal materials are processed quickly, only minor damage must be left on the layer to create a CRASH PAD where the cut surface is not visible from the outside. The key is to process only what is needed and leave the calculated remaining amount.
< 0.15mm
< 0.05mm
< 0.6mm
> 85%
Core Technology
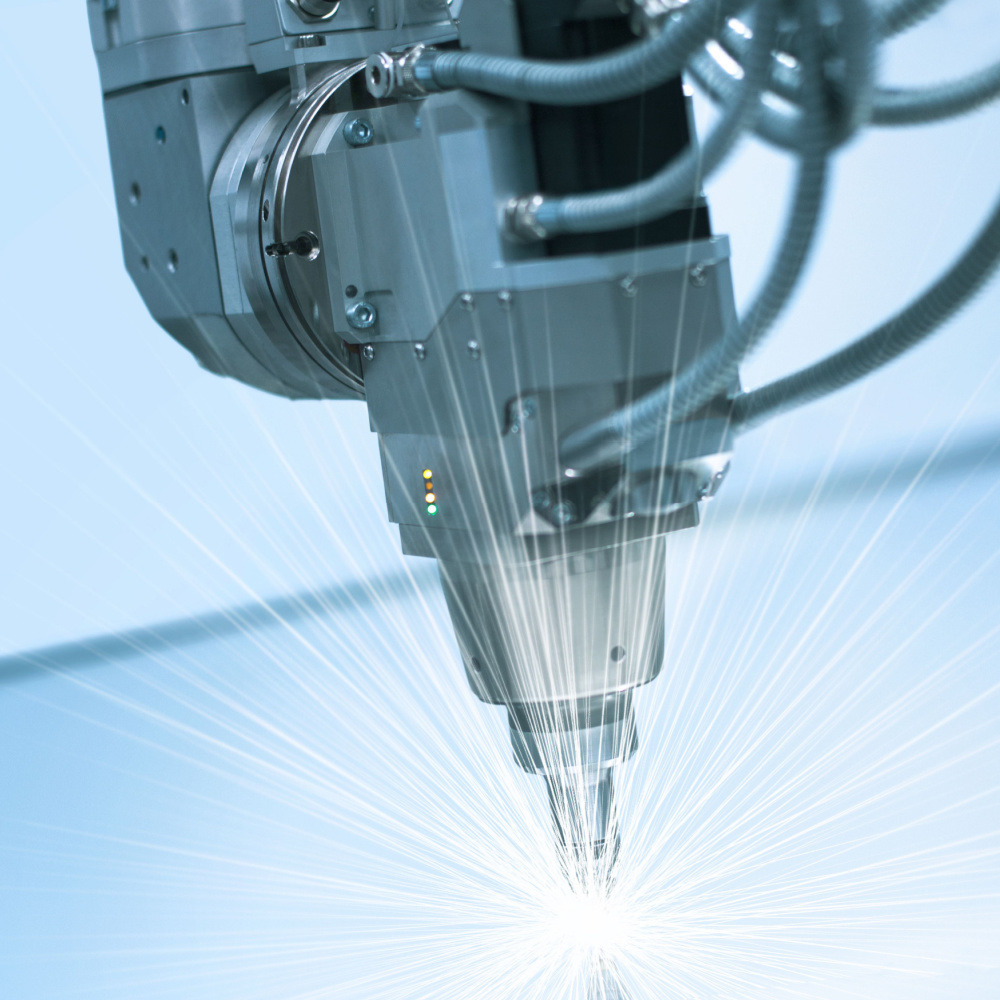
productivity
Unlike physical cutting methods, lasers do not reduce quality due to wear and tear. Consistent results are maintained for every lot while maintaining the same processability at all times. Furthermore, thanks to the non-contact method, no residue is generated.
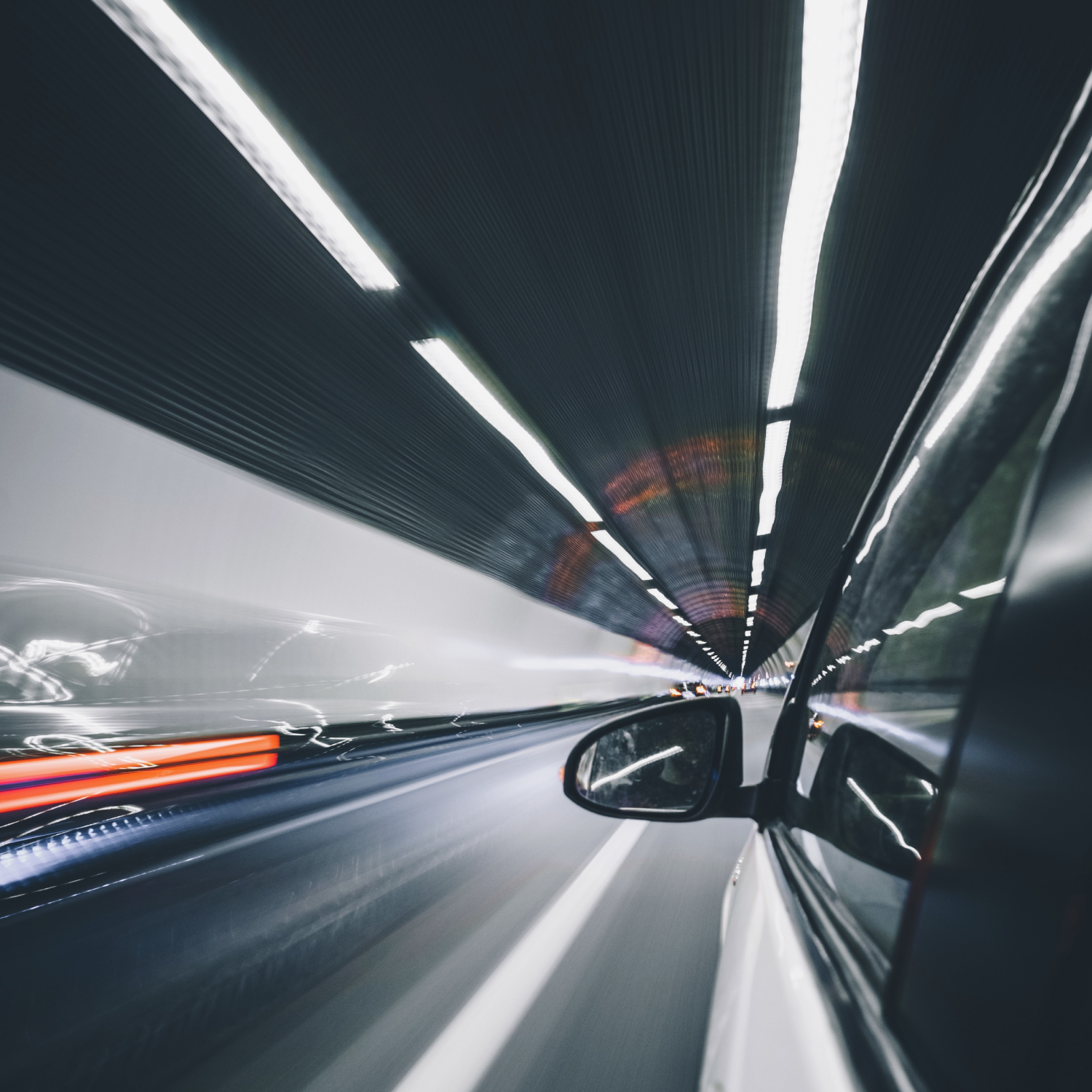
predictability
CRASH PAD is the most important safety device for drivers, and scoring must be performed at a set depth. The most commonly used physical cutting method makes it difficult to achieve predictable quality because the result after processing is unknown. Reduce quality costs and increase device reliability with laser systems that enable real-time feedback.
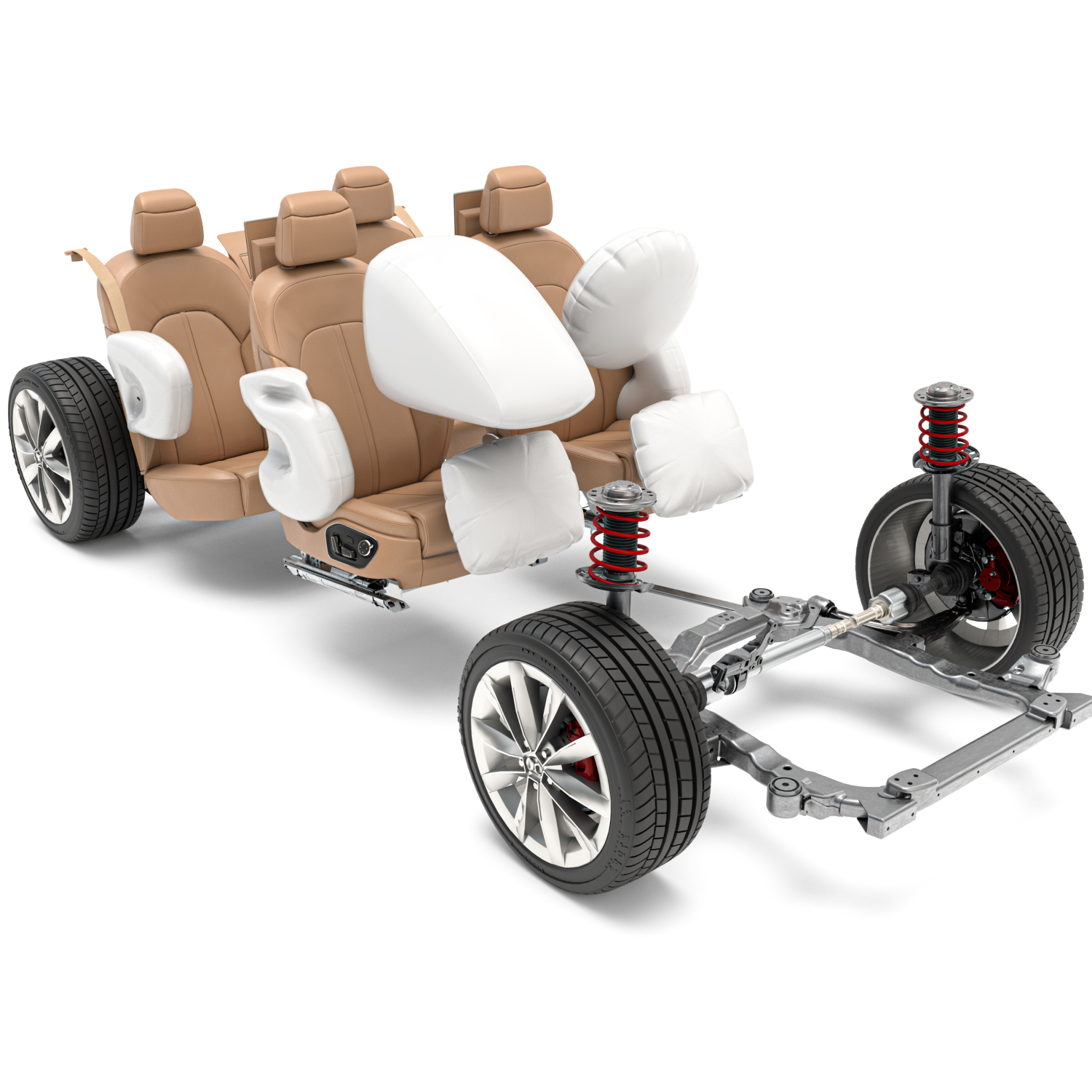
versatility
Laser scoring achieves a quality suitable for various environments requiring safety devices by achieving error accuracy in the order of a few microunits. Since it can work flexibly at 360 degrees, it can be applied not only to passenger seats, but also to various designs such as driver seats and side curtains.
Core Technology
Heading
Lorem ipsum dolor sit amet, consectetur adipiscing elit. Suspendisse varius enim in eros elementum tristique. Duis cursus, mi quis viverra ornare, eros dolor interdum nulla, ut commodo diam libero vitae erat. Aenean faucibus nibh et justo cursus id rutrum lorem imperdiet. Nunc ut sem vitae risus tristique posuere.
Heading
Lorem ipsum dolor sit amet, consectetur adipiscing elit. Suspendisse varius enim in eros elementum tristique. Duis cursus, mi quis viverra ornare, eros dolor interdum nulla, ut commodo diam libero vitae erat. Aenean faucibus nibh et justo cursus id rutrum lorem imperdiet. Nunc ut sem vitae risus tristique posuere.
Heading
Lorem ipsum dolor sit amet, consectetur adipiscing elit. Suspendisse varius enim in eros elementum tristique. Duis cursus, mi quis viverra ornare, eros dolor interdum nulla, ut commodo diam libero vitae erat. Aenean faucibus nibh et justo cursus id rutrum lorem imperdiet. Nunc ut sem vitae risus tristique posuere.
Heading
Lorem ipsum dolor sit amet, consectetur adipiscing elit. Suspendisse varius enim in eros elementum tristique. Duis cursus, mi quis viverra ornare, eros dolor interdum nulla, ut commodo diam libero vitae erat. Aenean faucibus nibh et justo cursus id rutrum lorem imperdiet. Nunc ut sem vitae risus tristique posuere.