Busbar connection welding
In order for multiple cells to be combined into a battery module, highly conductive bus bars such as aluminum and copper must connect the cells into a single assembly. Although the initial cost is high compared to other methods, lasers are superior in energy efficiency and low maintenance costs. In particular, since consistent quality work is performed at a high speed, it shows excellent productivity for connecting bus bars and terminals, which increase exponentially with the size of the module.
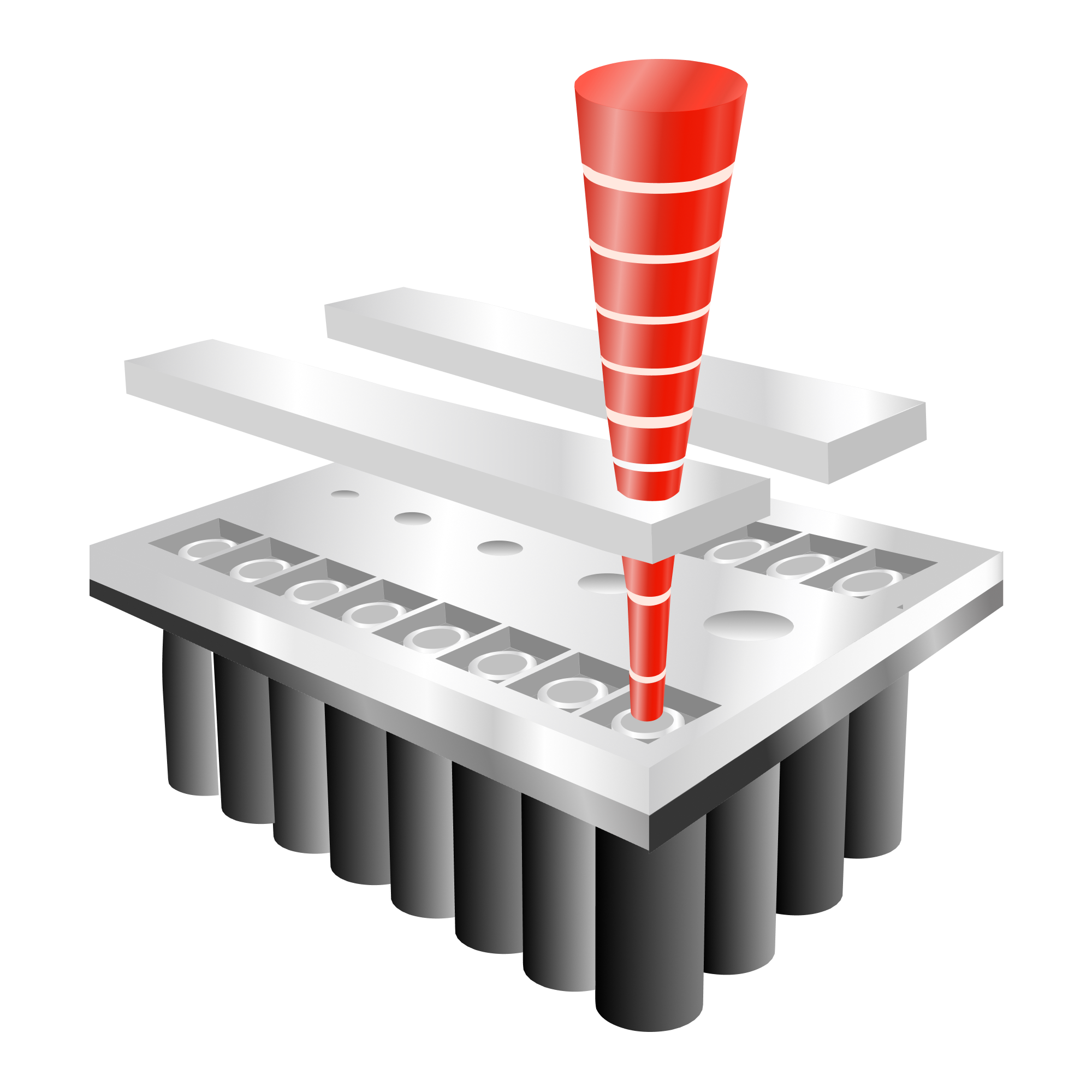
Features
integrity
Even cells made with advanced materials and innovative designs can be less energy efficient due to the electrical resistance of the bus bar. The laser, which injects concentrated energy at the correct position, promotes stable keyhole formation and melting to control porosity and motion. Laser integrity welding optimizes the bus bar's conductivity and heat generation.
FAST WOBBLE
If the gap between the busbar connections is wide, can't they be welded with a laser? With WOBBLE technology implemented as a high-speed scanning mirror and laser parameter optimization, it is possible to join even areas larger than the spot. Welding of dissimilar materials is completed without large amounts of plasma gas, contaminating filler materials, and high-wavelength lasers.
Intuitive controls
As standards for energy efficiency and stability are strengthened, the design of battery modules will also continue to change. Since laser systems can be programmed intuitively, they are easy to respond to various changes in design and process. Even module lines that are already in production can be switched with minimal production interruptions.
integrity
Even cells made with advanced materials and innovative designs can be less energy efficient due to the electrical resistance of the bus bar. The laser, which injects concentrated energy at the correct position, promotes stable keyhole formation and melting to control porosity and motion. Laser integrity welding optimizes the bus bar's conductivity and heat generation.
FAST WOBBLE
If the gap between the busbar connections is wide, can't they be welded with a laser? With WOBBLE technology implemented as a high-speed scanning mirror and laser parameter optimization, it is possible to join even areas larger than the spot. Welding of dissimilar materials is completed without large amounts of plasma gas, contaminating filler materials, and high-wavelength lasers.
Intuitive controls
As standards for energy efficiency and stability are strengthened, the design of battery modules will also continue to change. Since laser systems can be programmed intuitively, they are easy to respond to various changes in design and process. Even module lines that are already in production can be switched with minimal production interruptions.
Robust
Real time
minimum
360°
Core Technology
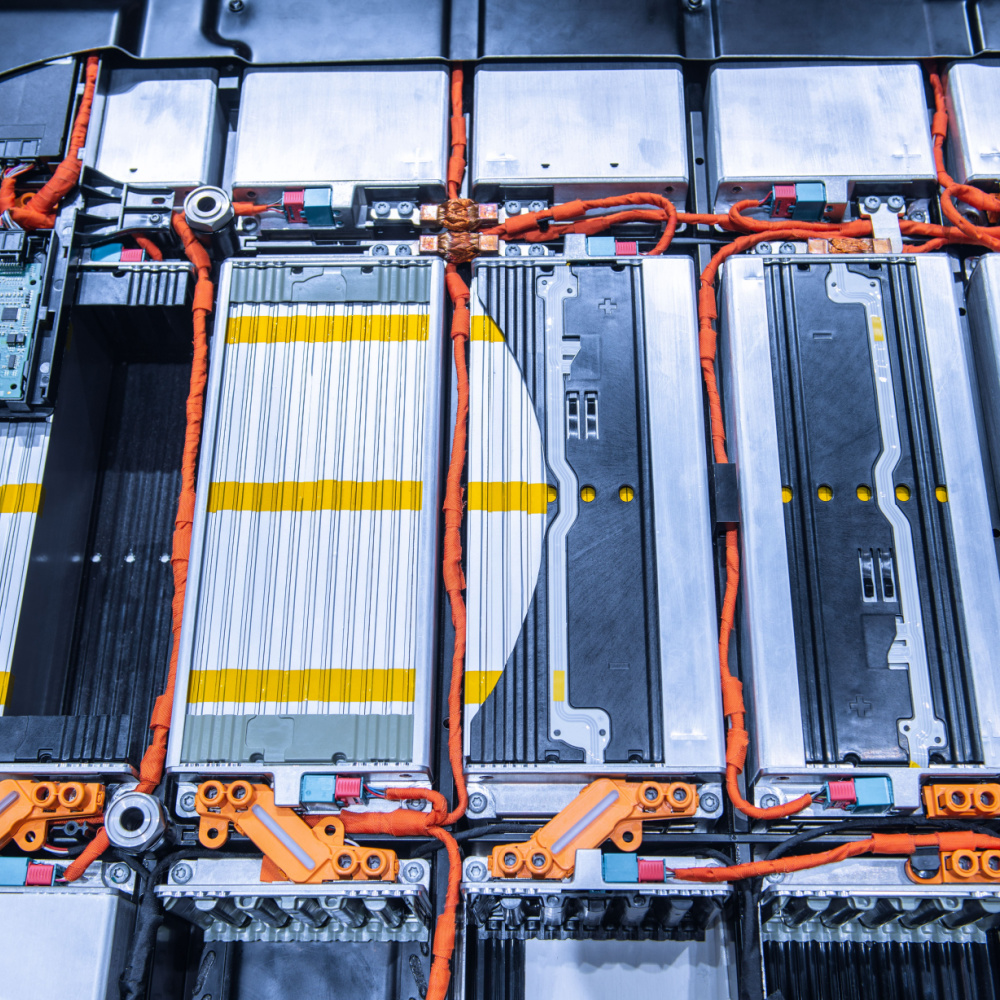
Tailored Pattern
The processing method must vary depending on the cell shape such as PRISMATIC, POUCH, and POUCH, as well as the position and shape of the bus bar attached to the battery module. The laser system can implement various methods such as FILLET JOINT, LAP JOINT, and MULTIPLE SPOT without changing the configuration. K2 designs and combines patterns considering not only the characteristics of materials, but also the quality and productivity required by customers.
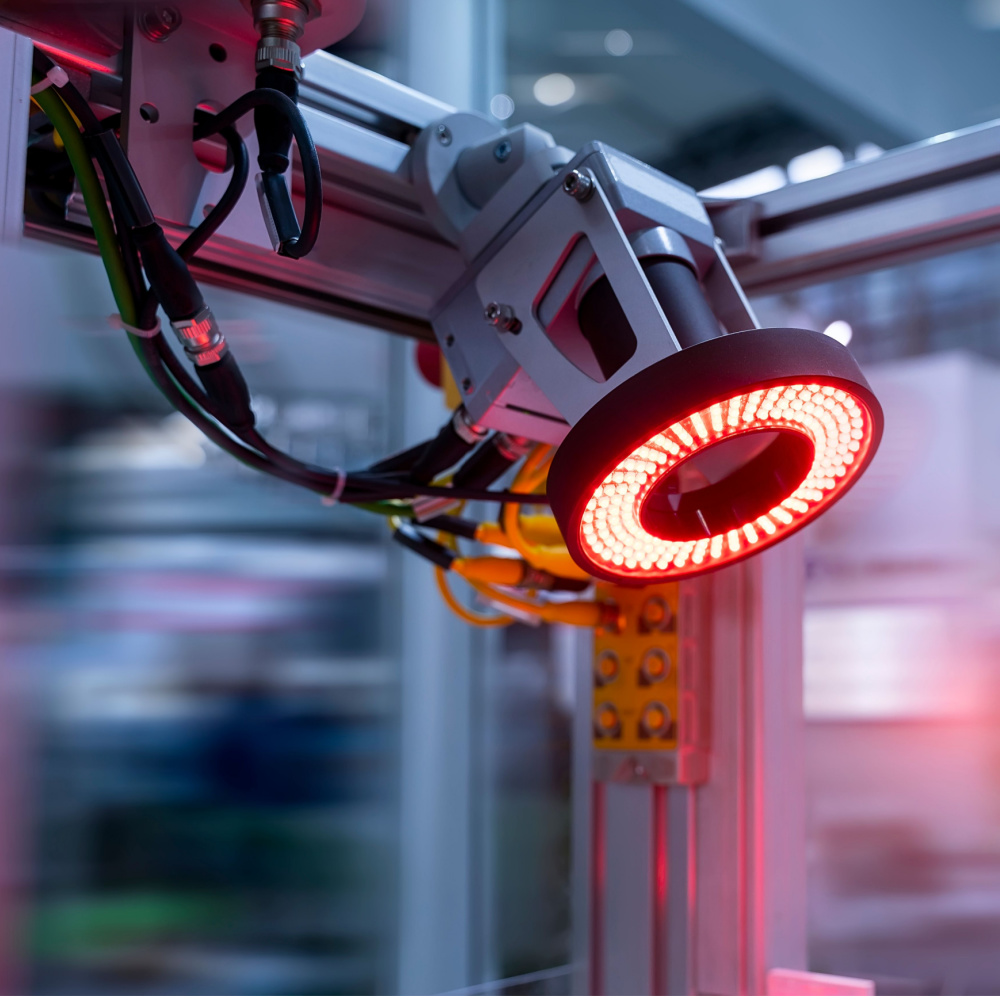
Vision monitoring and analysis
Since lasers accumulate energy in one area, it is very important to accurately identify even small position changes. To prevent beam positioning errors due to manufacturing tolerances and clamping errors in the busbar seat, a vision monitoring system detects deviations and variations. Monitoring before welding improves the accuracy of processing points, and monitoring after welding becomes important data for quality judgment.
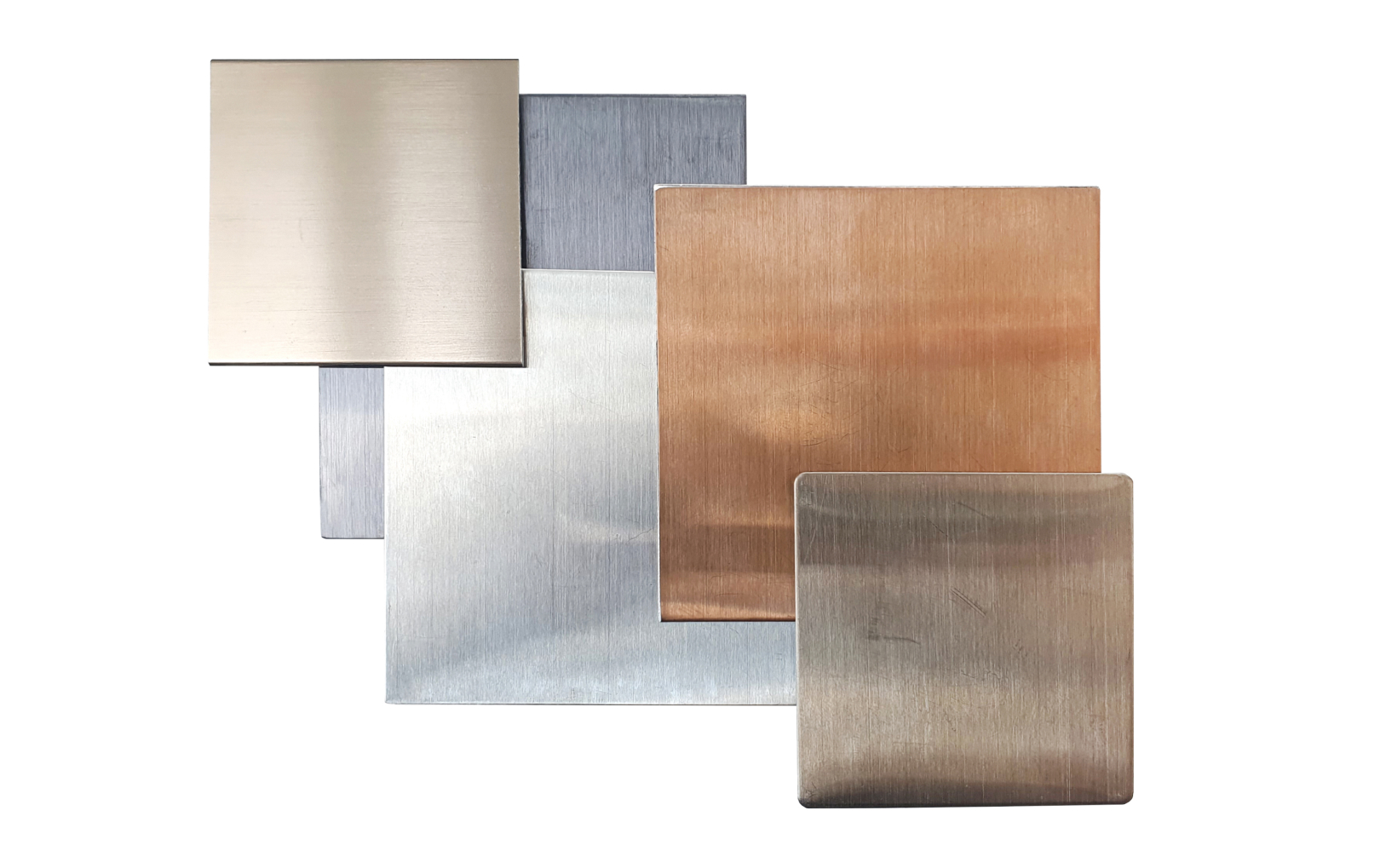
Material processing versatility
The laser system has good compatibility and can process various materials such as metal, plastic, and ceramics. Since battery bus bars can be made of various materials for each divided area such as TOP, SIDE, and BOTTOM, laser welding is commonly used.
Core Technology
Heading
Lorem ipsum dolor sit amet, consectetur adipiscing elit. Suspendisse varius enim in eros elementum tristique. Duis cursus, mi quis viverra ornare, eros dolor interdum nulla, ut commodo diam libero vitae erat. Aenean faucibus nibh et justo cursus id rutrum lorem imperdiet. Nunc ut sem vitae risus tristique posuere.
Heading
Lorem ipsum dolor sit amet, consectetur adipiscing elit. Suspendisse varius enim in eros elementum tristique. Duis cursus, mi quis viverra ornare, eros dolor interdum nulla, ut commodo diam libero vitae erat. Aenean faucibus nibh et justo cursus id rutrum lorem imperdiet. Nunc ut sem vitae risus tristique posuere.
Heading
Lorem ipsum dolor sit amet, consectetur adipiscing elit. Suspendisse varius enim in eros elementum tristique. Duis cursus, mi quis viverra ornare, eros dolor interdum nulla, ut commodo diam libero vitae erat. Aenean faucibus nibh et justo cursus id rutrum lorem imperdiet. Nunc ut sem vitae risus tristique posuere.
Heading
Lorem ipsum dolor sit amet, consectetur adipiscing elit. Suspendisse varius enim in eros elementum tristique. Duis cursus, mi quis viverra ornare, eros dolor interdum nulla, ut commodo diam libero vitae erat. Aenean faucibus nibh et justo cursus id rutrum lorem imperdiet. Nunc ut sem vitae risus tristique posuere.