Sylindrical battery cell
Terminal welding after insertion of JELLY ROLL and sealing after FIXTE filling are performed. Cylindrical cells have very thin sheets, so if the depth is not precisely controlled, the material as well as the inside of the cell will be damaged. The keyhole created by the fiber laser's fine spot can perform the liquefaction and cooling process of the metal very quickly while minimizing unnecessary deformation.
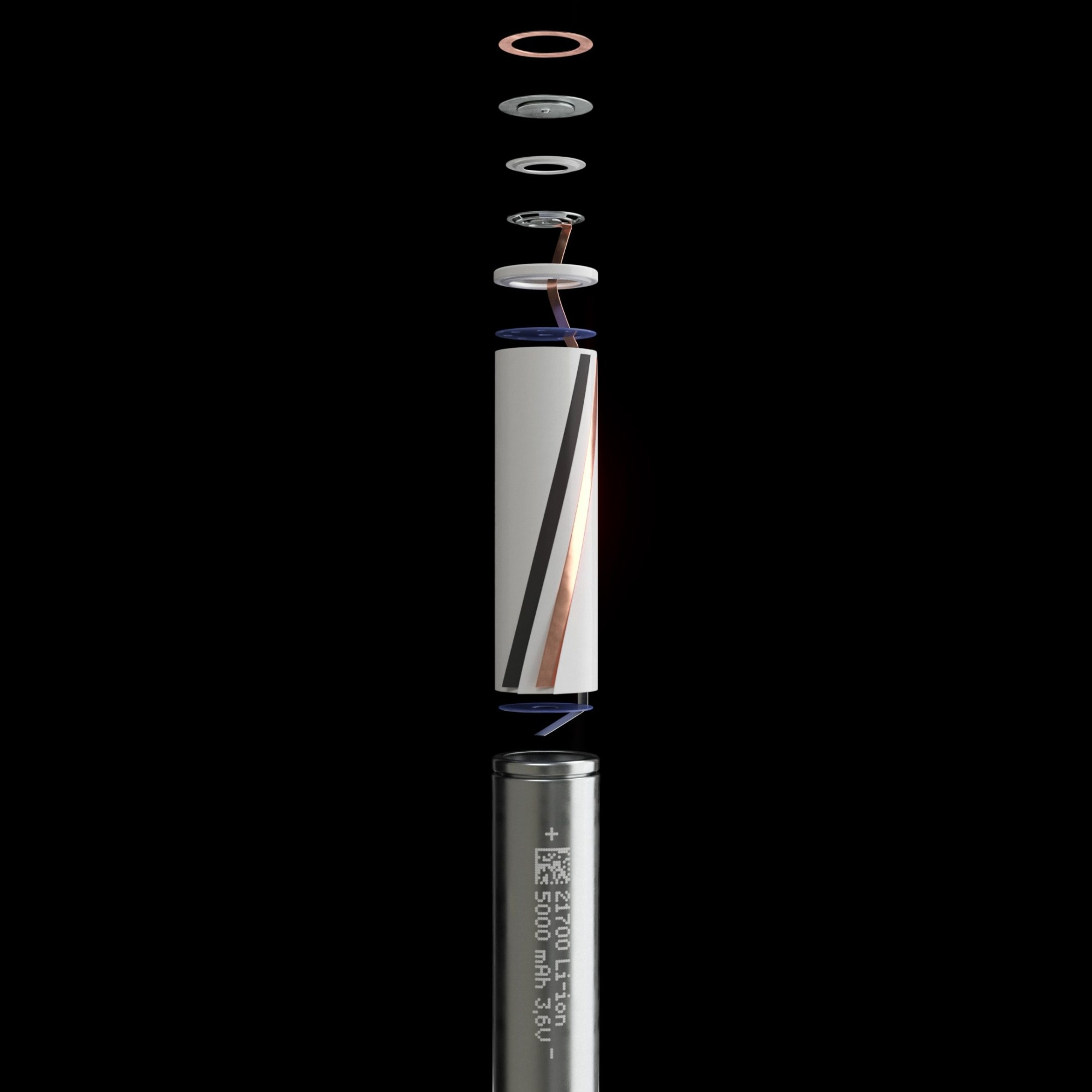
Features
Minimize shaking
Cylindrical cells must be evenly filled with a uniform weight of TE. Laser systems that perform non-contact welding by moving energy spots can minimize cell shaking compared to CRIMPING and BEADING methods where there is a lot of mechanical contact.
Fast Geometry
Cylindrical cells surrounded by rigid cylinder cans can be stacked in various shapes to uniformly adjust the size and shape of the product. However, since they are small and round, the number and complexity of welds increases exponentially compared to square shapes and pouches. Equipped with a high-speed scanner, K2's CAP WELDING solution performs fast and accurate welding processes with excellent energy GEOMETRY.
SMART FOCAL SYSTEM
The fatal and only weakness of laser welding is that it is focus-sensitive. If the processing error and position deviation of SHELL are severe, weak welding will occur beyond the optical DOF. With the SMART FOCAL SYSTEM, which measures the height of the workpiece and adjusts the focus, K2's CAP WELDING SYSTEM solved the laser's last weakness.
Minimize shaking
Cylindrical cells must be evenly filled with a uniform weight of TE. Laser systems that perform non-contact welding by moving energy spots can minimize cell shaking compared to CRIMPING and BEADING methods where there is a lot of mechanical contact.
Fast Geometry
Cylindrical cells surrounded by rigid cylinder cans can be stacked in various shapes to uniformly adjust the size and shape of the product. However, since they are small and round, the number and complexity of welds increases exponentially compared to square shapes and pouches. Equipped with a high-speed scanner, K2's CAP WELDING solution performs fast and accurate welding processes with excellent energy GEOMETRY.
SMART FOCAL SYSTEM
The fatal and only weakness of laser welding is that it is focus-sensitive. If the processing error and position deviation of SHELL are severe, weak welding will occur beyond the optical DOF. With the SMART FOCAL SYSTEM, which measures the height of the workpiece and adjusts the focus, K2's CAP WELDING SYSTEM solved the laser's last weakness.
0.2-0.4
0.2-0.6
Good
ZERO
Core Technology
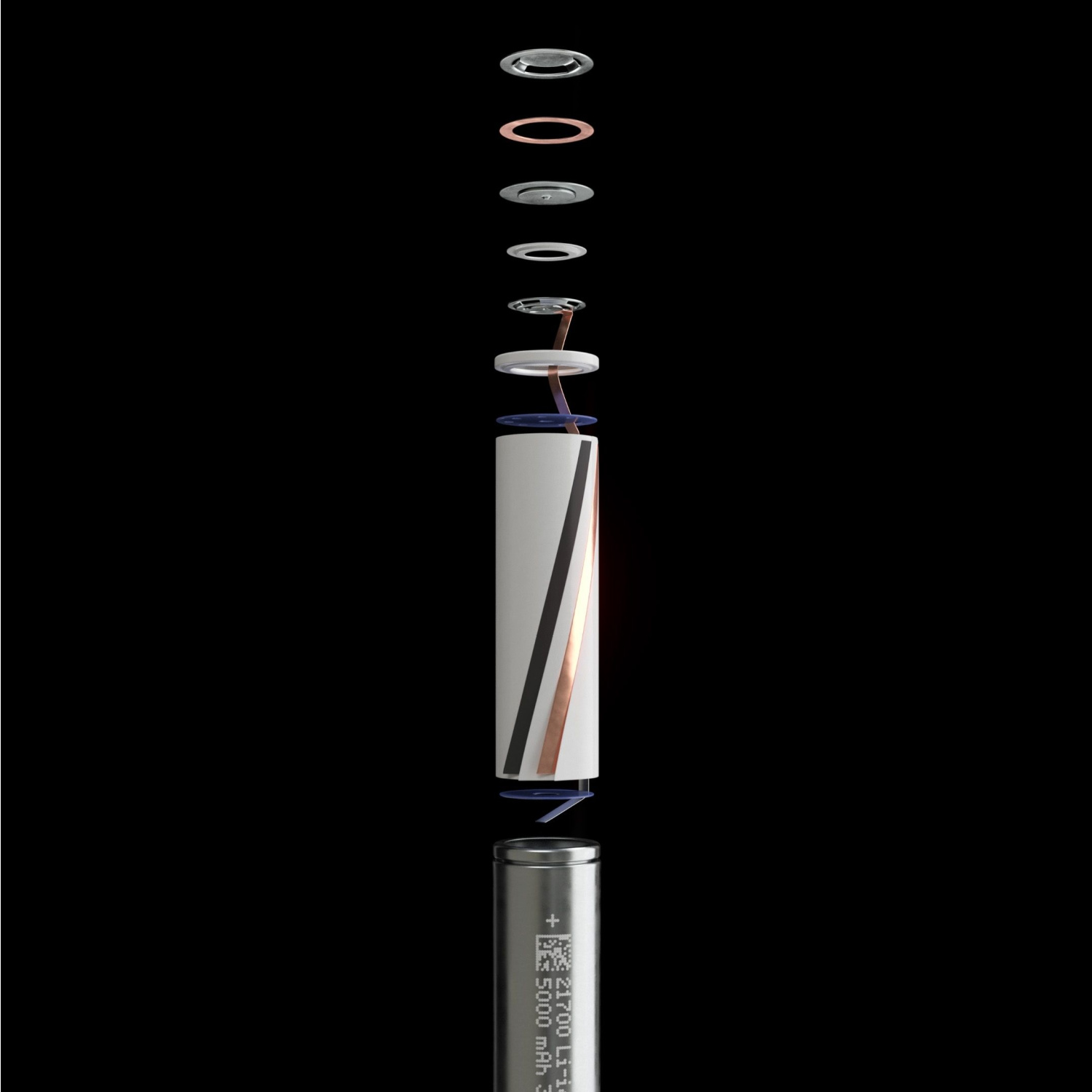
Quality inspection
Incorrect welding causes uneven loading between cells, and it becomes very difficult to check and correct defects after they are combined into a module or pack. Therefore, it is necessary to explore SHELL's welding line before processing and check the CAP WELDING status after processing. K2 supports customers to establish correct quality standards based on inspection data and experience accumulated over many years.
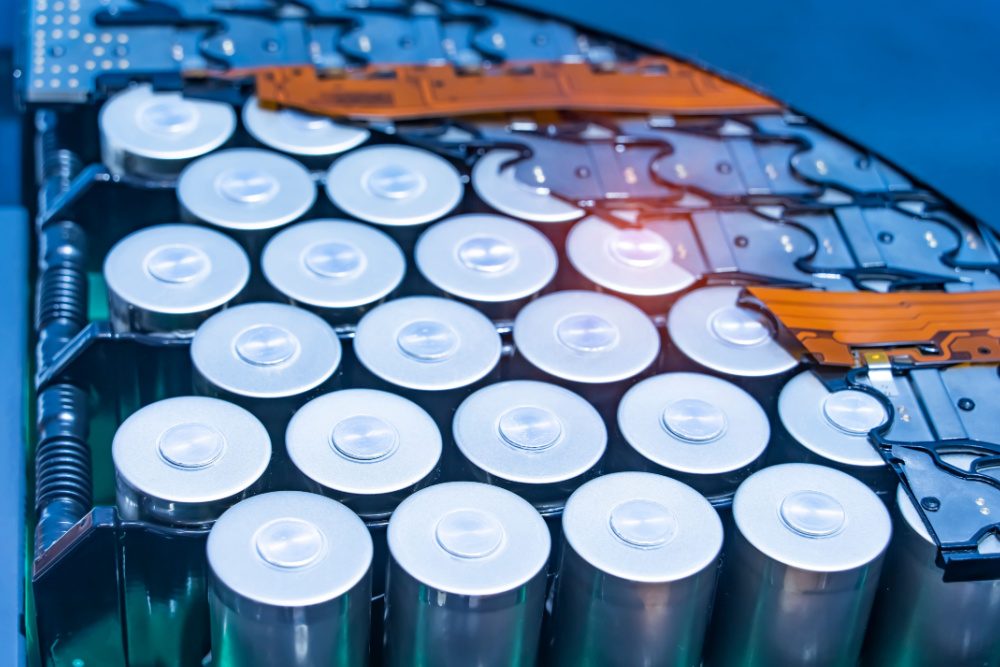
multibeam
Most of the cells used in POWER BATTERY are made of very thin aluminum with sides, cover, and bottom of 0.8 mm or less to reduce weight. Since aluminum has a very fast cooling rate after laser welding, pores caused by hydrogen and air bubbles easily occur. Furthermore, due to the nature of alloys, defect purification and liquefaction that occur at high temperatures cause a decrease in bonding strength due to cracking. The laser profile must be shaped and an optimal energy distribution must be created so that a stable welding response can proceed.
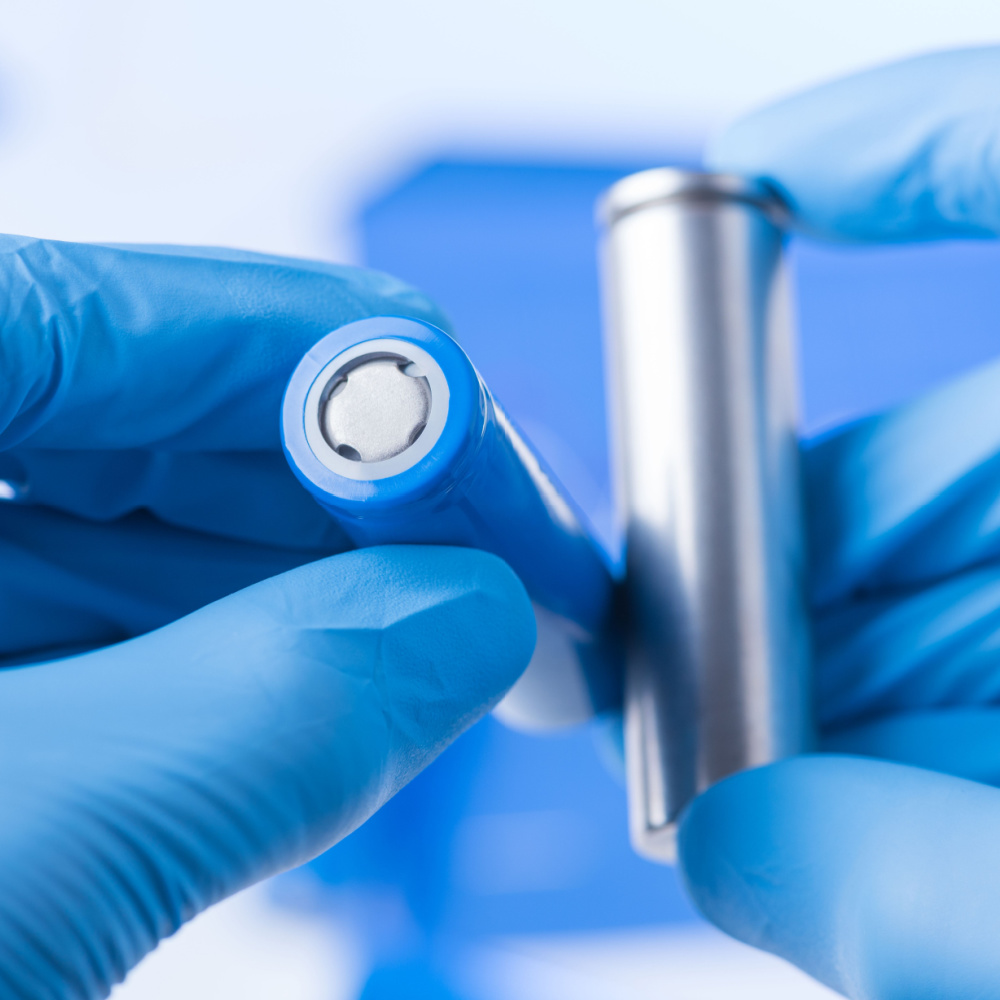
Facility stability
Enhancing processing quality is important, but maintaining consistent quality is also very important. Lasers can perform delicate and powerful welds, but care must be taken to avoid damaging the optical system. From hardware to optical systems, such as installing lens filters, adjusting the beam transmission angle, and changing the focus level, K2 takes all the methods for stable business operations for customers.
Core Technology
Heading
Lorem ipsum dolor sit amet, consectetur adipiscing elit. Suspendisse varius enim in eros elementum tristique. Duis cursus, mi quis viverra ornare, eros dolor interdum nulla, ut commodo diam libero vitae erat. Aenean faucibus nibh et justo cursus id rutrum lorem imperdiet. Nunc ut sem vitae risus tristique posuere.
Heading
Lorem ipsum dolor sit amet, consectetur adipiscing elit. Suspendisse varius enim in eros elementum tristique. Duis cursus, mi quis viverra ornare, eros dolor interdum nulla, ut commodo diam libero vitae erat. Aenean faucibus nibh et justo cursus id rutrum lorem imperdiet. Nunc ut sem vitae risus tristique posuere.
Heading
Lorem ipsum dolor sit amet, consectetur adipiscing elit. Suspendisse varius enim in eros elementum tristique. Duis cursus, mi quis viverra ornare, eros dolor interdum nulla, ut commodo diam libero vitae erat. Aenean faucibus nibh et justo cursus id rutrum lorem imperdiet. Nunc ut sem vitae risus tristique posuere.
Heading
Lorem ipsum dolor sit amet, consectetur adipiscing elit. Suspendisse varius enim in eros elementum tristique. Duis cursus, mi quis viverra ornare, eros dolor interdum nulla, ut commodo diam libero vitae erat. Aenean faucibus nibh et justo cursus id rutrum lorem imperdiet. Nunc ut sem vitae risus tristique posuere.