Square battery cell
In the case of a rectangular battery, it has a relatively stable structure for internal gas pressure. Since there are no restrictions on the choice of anode, cathode, and electrolyte materials, they have the advantage of greater room for energy density improvement and can be more easily combined into battery modules compared to cylindrical ones.
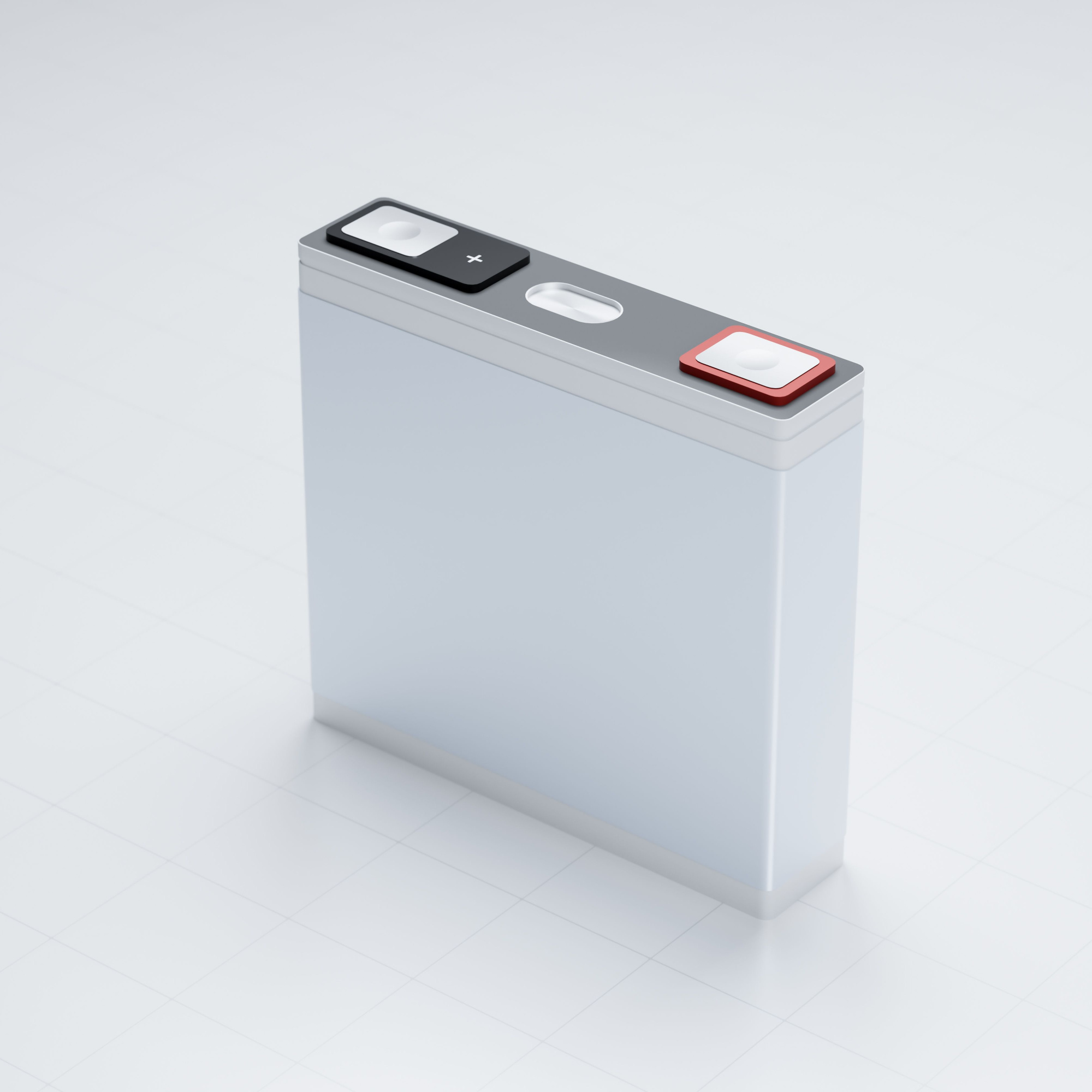
Features
Top weld
Fit the square cover with ANODE TAB to the top end of the SHELL and join the cover and SHELL. While the laser is emitted from a fixed position, the worktable equipped with the cell moves and welding is performed. Since tolerances and position accuracy between the cover and SHELL are very important, it is important to locate the starting edge and track the weld line with vision.
Side weld
In addition to having a wider tolerance range compared to the top processing method, there is also less possibility that scattering products will invade the SHELL COVER. However, since there is a risk that the cover will swell after welding and affect subsequent processes, heat collection caused by high-power lasers must be effectively controlled.
Safety Vent
It is a thin metal plate on top of the SEAL PLATE, and if the internal pressure exceeds a certain level, it will crack to prevent the battery from bursting. It may seem like a simple process of welding two metal sheets, but it is a difficult task that requires not only perfect sealing, but also making the weld stronger than a metal sheet.
Top weld
Fit the square cover with ANODE TAB to the top end of the SHELL and join the cover and SHELL. While the laser is emitted from a fixed position, the worktable equipped with the cell moves and welding is performed. Since tolerances and position accuracy between the cover and SHELL are very important, it is important to locate the starting edge and track the weld line with vision.
Side weld
In addition to having a wider tolerance range compared to the top processing method, there is also less possibility that scattering products will invade the SHELL COVER. However, since there is a risk that the cover will swell after welding and affect subsequent processes, heat collection caused by high-power lasers must be effectively controlled.
Safety Vent
It is a thin metal plate on top of the SEAL PLATE, and if the internal pressure exceeds a certain level, it will crack to prevent the battery from bursting. It may seem like a simple process of welding two metal sheets, but it is a difficult task that requires not only perfect sealing, but also making the weld stronger than a metal sheet.
SEALING PIN
Various types of products are used. Separate pretreatment is required to prevent cracking due to cooling hardening and residual stress; in particular, residual electrolyte crystals can cause spatter and pores. Both surface cleaning and welding can be performed with a high-speed pulsed laser.
Multi
compact
Easy
High
Core Technology
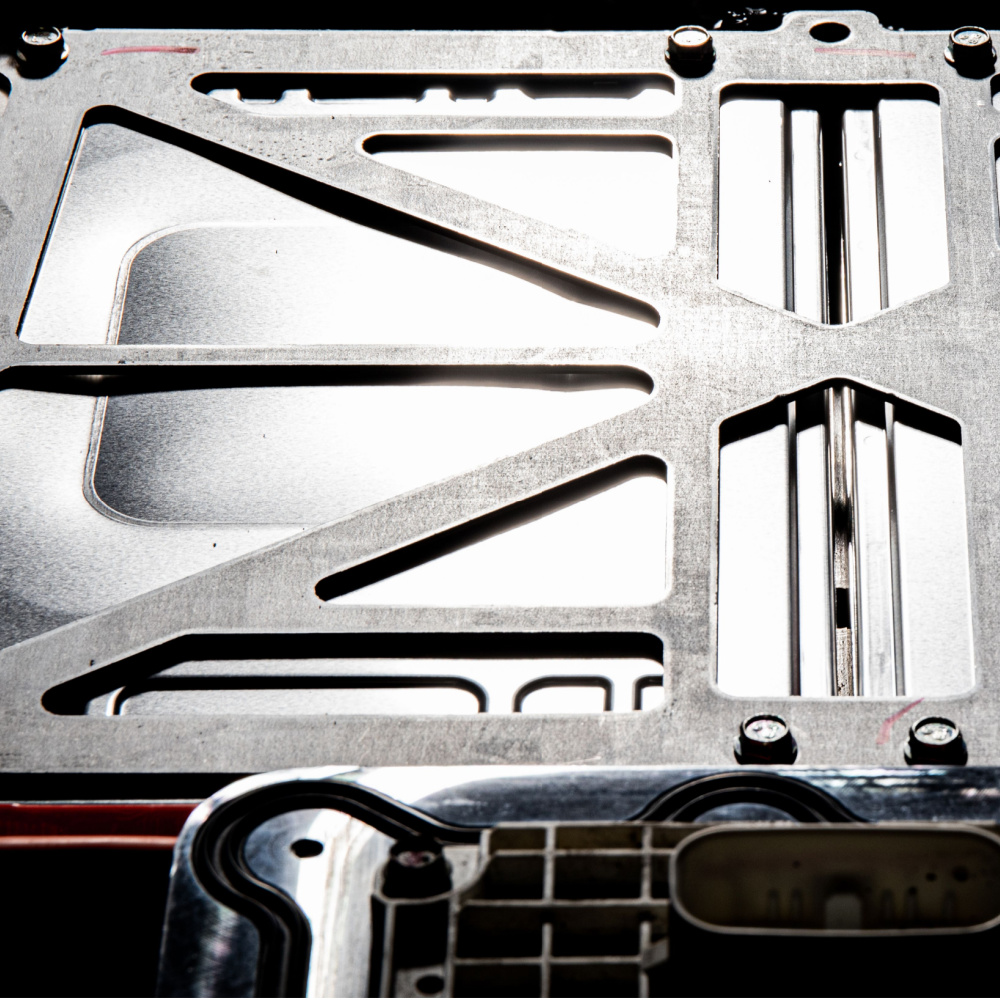
Integrated welding
Since electrical components for driving a prismatic battery (PRISMATIC BATTERY) are already inserted into the housing, care must be taken not to affect the internal structure when performing Casing WELDING. Lasers with high energy concentration are beneficial in maintaining product stability by minimizing thermal effects and warping caused by welding.
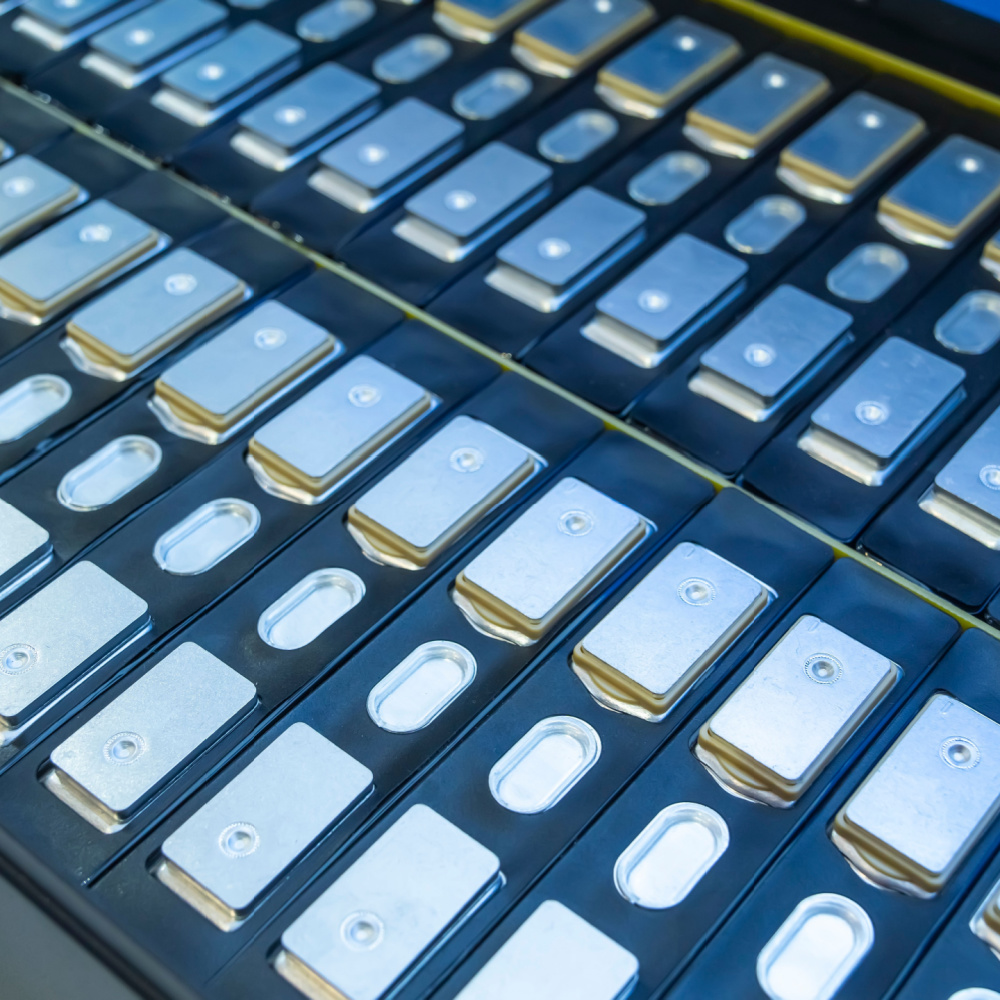
Exact location
To minimize internal effects on battery cells, you might think that welding on the edge should be performed as much as possible. However, this method rather weakens the connection and cannot meet the quality standards required to withstand extreme temperatures, vibrations, and electrical loads. The K2's laser system is equipped with a vision sensor to search for points where optimal weld joints are made.
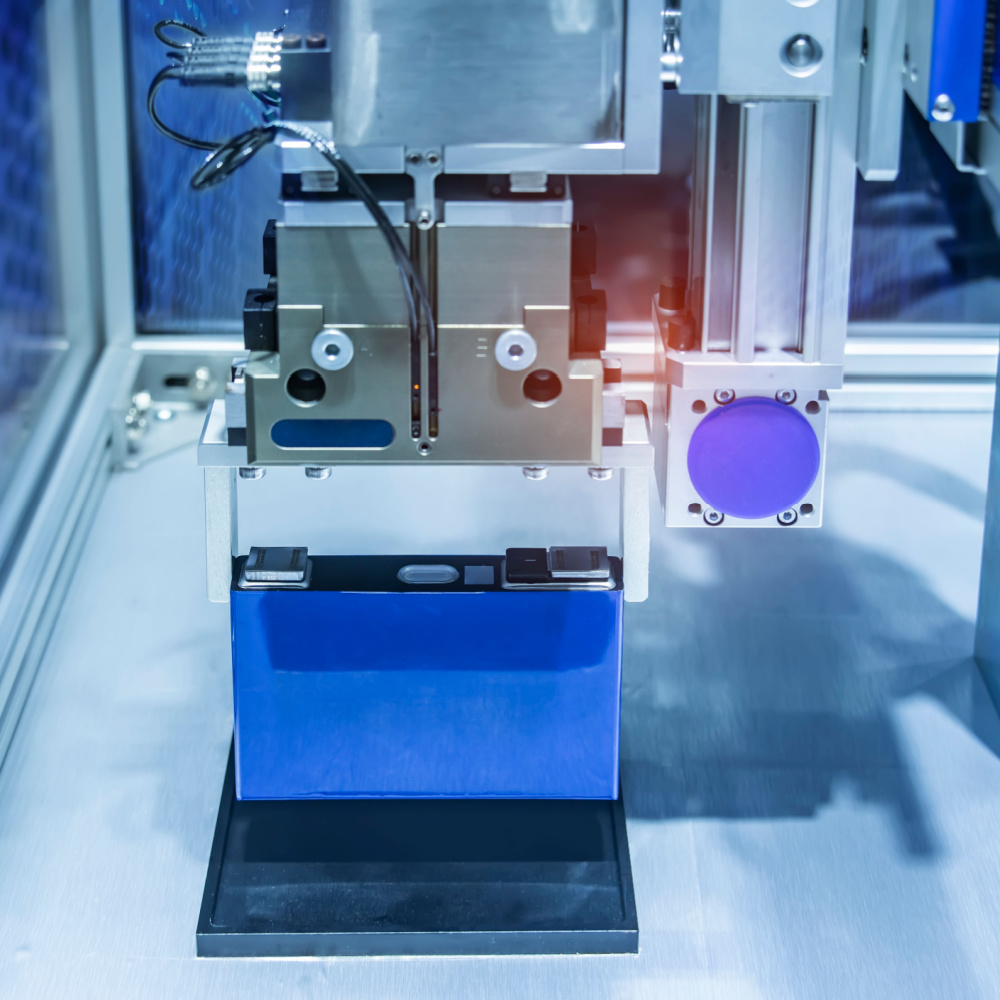
One-step machining
Various components, such as explosion-proof valves, flip chips, poles, liquid injection hole nails, and seals, must be built into or attached to the case for normal operation and safety. The smoother the joint seam of the part, the more advantageous it is for normal function performance. The K2 is a high-speed precision scanner that performs seamless and smooth welds all at once without interruption.
Core Technology
Heading
Lorem ipsum dolor sit amet, consectetur adipiscing elit. Suspendisse varius enim in eros elementum tristique. Duis cursus, mi quis viverra ornare, eros dolor interdum nulla, ut commodo diam libero vitae erat. Aenean faucibus nibh et justo cursus id rutrum lorem imperdiet. Nunc ut sem vitae risus tristique posuere.
Heading
Lorem ipsum dolor sit amet, consectetur adipiscing elit. Suspendisse varius enim in eros elementum tristique. Duis cursus, mi quis viverra ornare, eros dolor interdum nulla, ut commodo diam libero vitae erat. Aenean faucibus nibh et justo cursus id rutrum lorem imperdiet. Nunc ut sem vitae risus tristique posuere.
Heading
Lorem ipsum dolor sit amet, consectetur adipiscing elit. Suspendisse varius enim in eros elementum tristique. Duis cursus, mi quis viverra ornare, eros dolor interdum nulla, ut commodo diam libero vitae erat. Aenean faucibus nibh et justo cursus id rutrum lorem imperdiet. Nunc ut sem vitae risus tristique posuere.
Heading
Lorem ipsum dolor sit amet, consectetur adipiscing elit. Suspendisse varius enim in eros elementum tristique. Duis cursus, mi quis viverra ornare, eros dolor interdum nulla, ut commodo diam libero vitae erat. Aenean faucibus nibh et justo cursus id rutrum lorem imperdiet. Nunc ut sem vitae risus tristique posuere.