Metal coil welding
As the electrification of vehicles accelerates, the number of motors used increases exponentially, and on average, 30 to 50 motors are used, and in the case of luxury cars, about 100 motors are used. In the press process for manufacturing motor cores, automatically connecting coils with a laser not only increases work continuity, but also contributes to improving cost competitiveness by reducing the amount of discarded scrap.
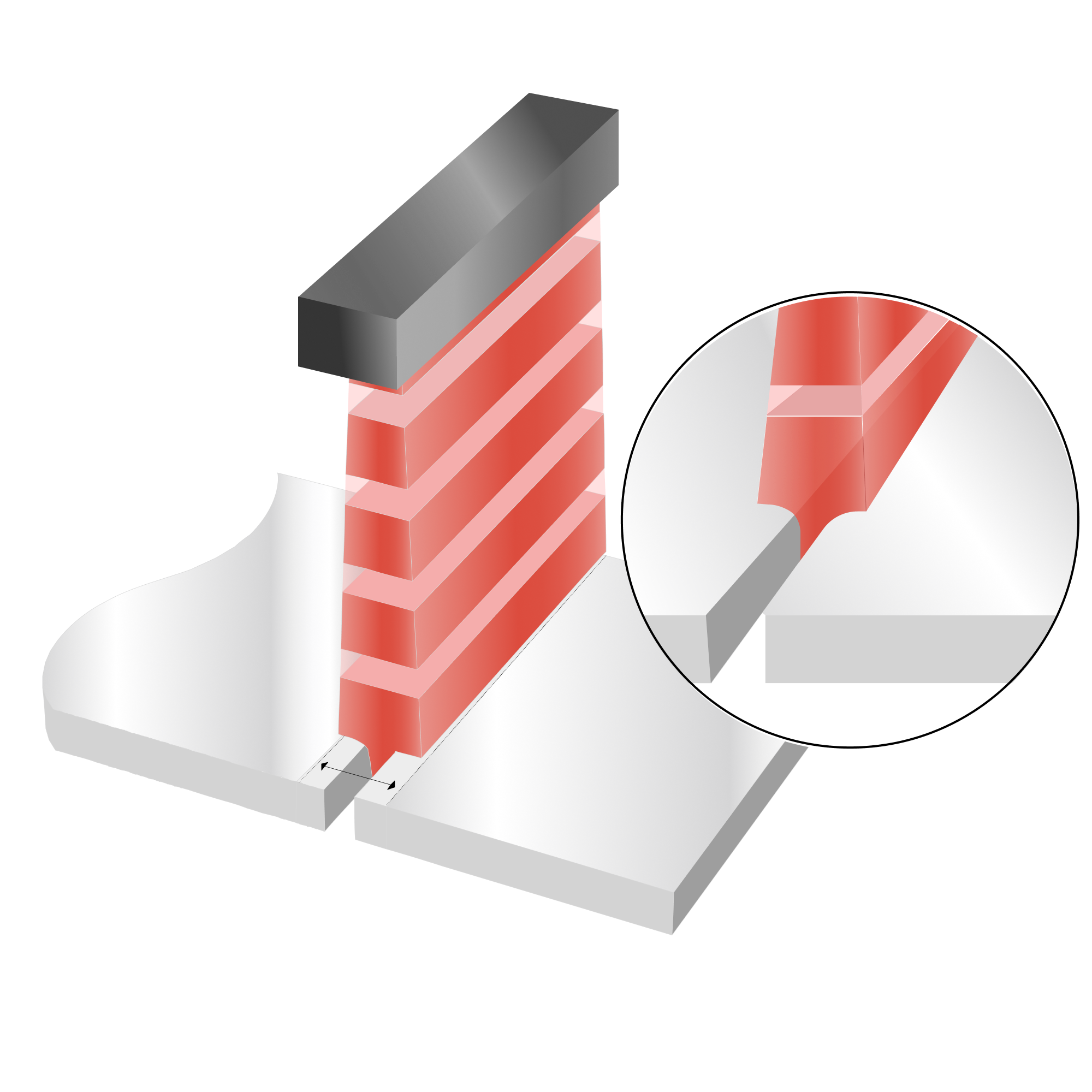
Features
Positioning
Align the tail of the leading coil with the head of the newly inserted trailing coil.
CUTTING
For proper butt welding, the tail of the leading corill and the head of the trailing coil are finely cut so that they fit together.
ALLENGAL
Proper welding is not possible if the gap between the joints becomes loose. Align the tail height and direction of the leading coil so that the two coils meet properly.
Positioning
Align the tail of the leading coil with the head of the newly inserted trailing coil.
CUTTING
For proper butt welding, the tail of the leading corill and the head of the trailing coil are finely cut so that they fit together.
ALLENGAL
Proper welding is not possible if the gap between the joints becomes loose. Align the tail height and direction of the leading coil so that the two coils meet properly.
WELDING
A high-speed laser is launched to connect the coils. A vision system is operated for accurate positioning and monitoring.
2kW
20um
5um
5um
Core Technology
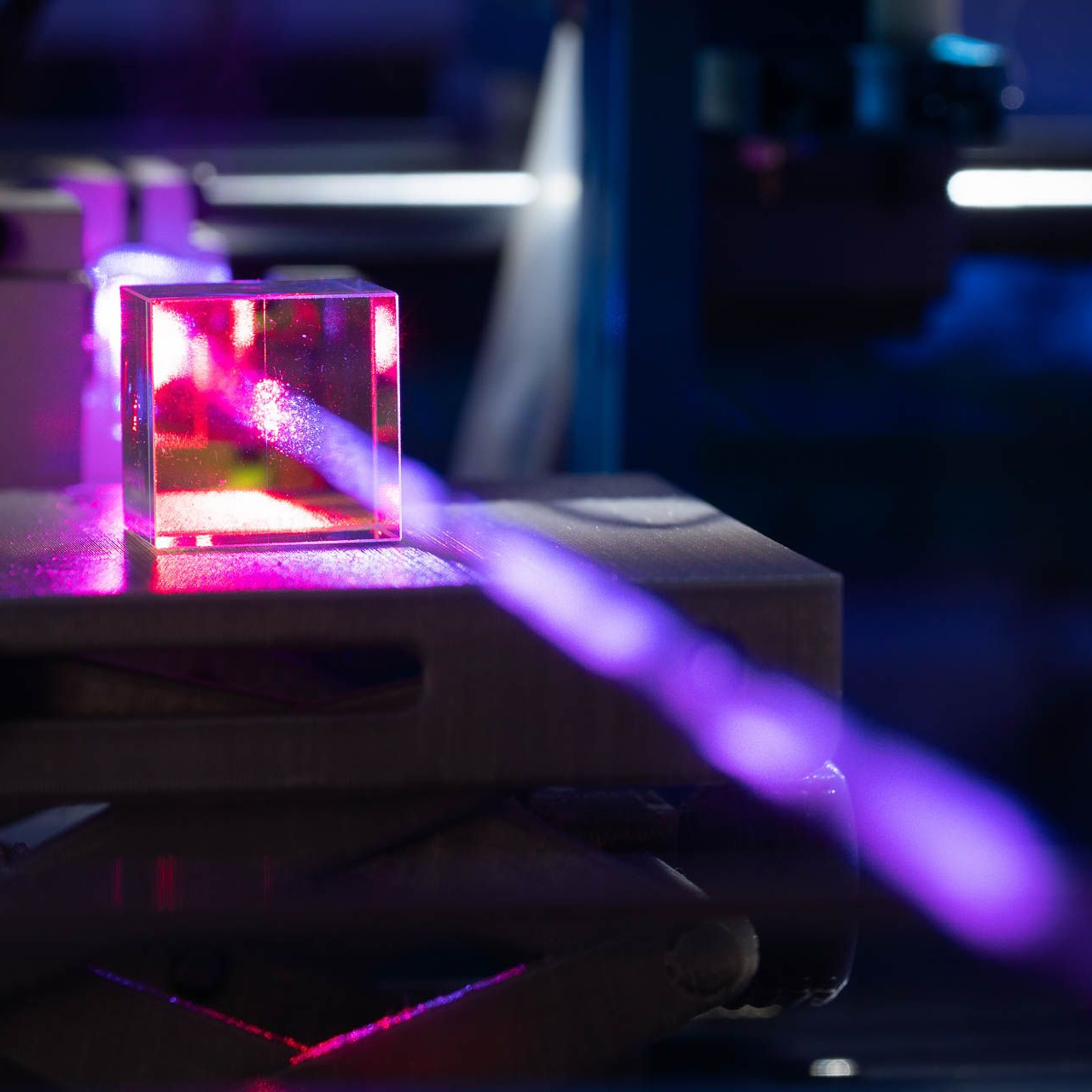
Line beam
Classic welding methods are difficult to meet the quality levels required by the market. Laser welding is also prone to warping when welding a thickness of 0.5 mm or less due to the uniform distribution of residual stress between the molten area and the heat-affected area. K2's proprietary LINE BEAM minimizes TEMPERATURE GRADIENT to suppress thermal expansion and improve quality.

Safe automation systems
Safety accidents can occur not only during sheet transportation and coil alignment processes, but also in the process of handling scrap generated by press molding. K2 implements an automated system equipped with a bead profile function so that a series of tasks can be performed accurately.
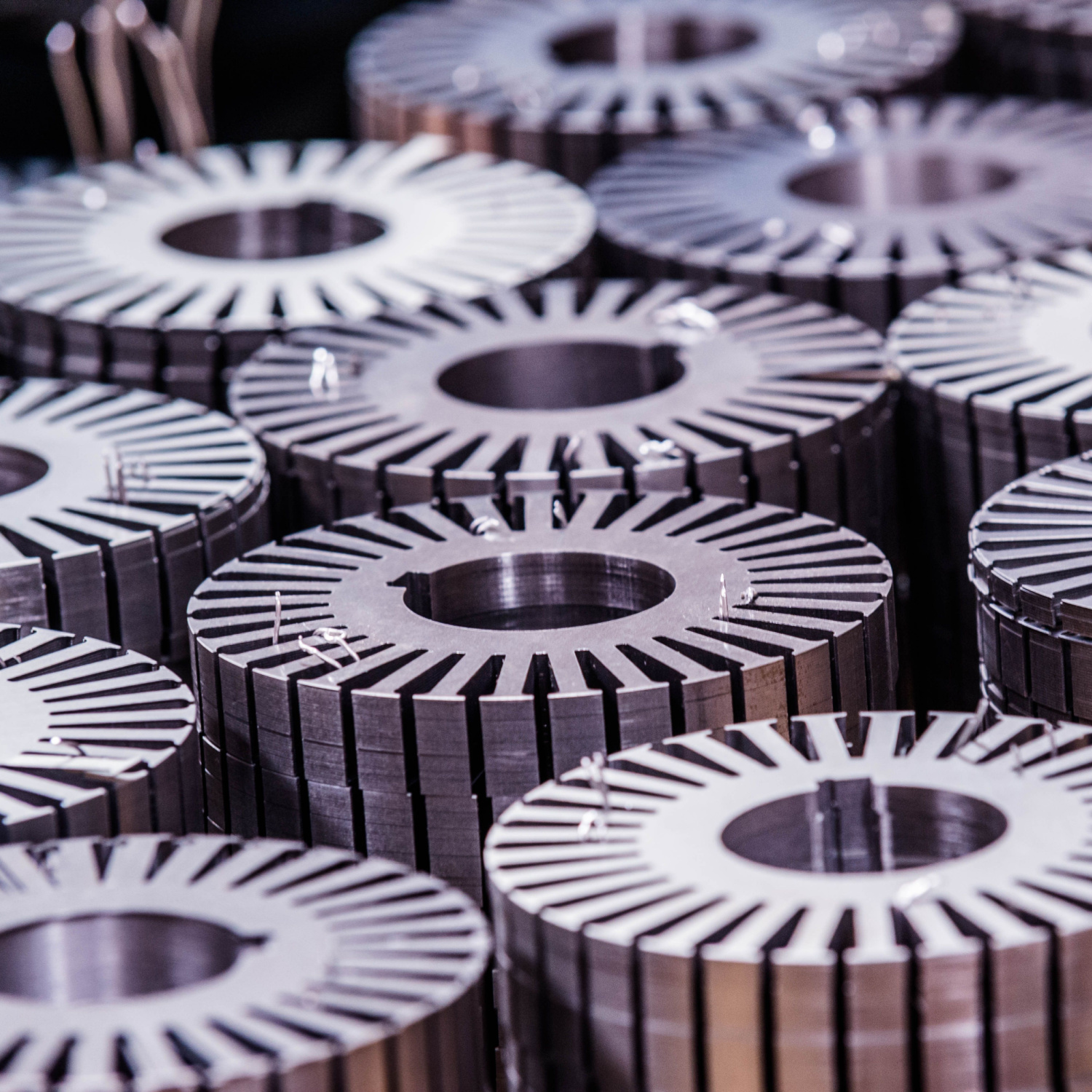
Maintaining the correct bead
When welding a 200 μm thick sheet, if the upper bead is not maintained at the 10 μm level, proper lamination will not be possible, which will affect the performance of the motor core. It is difficult to implement with conventional laser welding methods, but K2 solved this with its unique BEAM SHAPING technology.
Core Technology
Heading
Lorem ipsum dolor sit amet, consectetur adipiscing elit. Suspendisse varius enim in eros elementum tristique. Duis cursus, mi quis viverra ornare, eros dolor interdum nulla, ut commodo diam libero vitae erat. Aenean faucibus nibh et justo cursus id rutrum lorem imperdiet. Nunc ut sem vitae risus tristique posuere.
Heading
Lorem ipsum dolor sit amet, consectetur adipiscing elit. Suspendisse varius enim in eros elementum tristique. Duis cursus, mi quis viverra ornare, eros dolor interdum nulla, ut commodo diam libero vitae erat. Aenean faucibus nibh et justo cursus id rutrum lorem imperdiet. Nunc ut sem vitae risus tristique posuere.
Heading
Lorem ipsum dolor sit amet, consectetur adipiscing elit. Suspendisse varius enim in eros elementum tristique. Duis cursus, mi quis viverra ornare, eros dolor interdum nulla, ut commodo diam libero vitae erat. Aenean faucibus nibh et justo cursus id rutrum lorem imperdiet. Nunc ut sem vitae risus tristique posuere.
Heading
Lorem ipsum dolor sit amet, consectetur adipiscing elit. Suspendisse varius enim in eros elementum tristique. Duis cursus, mi quis viverra ornare, eros dolor interdum nulla, ut commodo diam libero vitae erat. Aenean faucibus nibh et justo cursus id rutrum lorem imperdiet. Nunc ut sem vitae risus tristique posuere.