Laser electrode notching
Notching is a process of molding a “tap (-: Anode, +: Cathode)” on the metal foil of an electrode that has been slitting. While the electrodes wound on the roll-to-roll equipment are continuously loosened, the laser shapes the notch at high speed according to the customer's desired design.
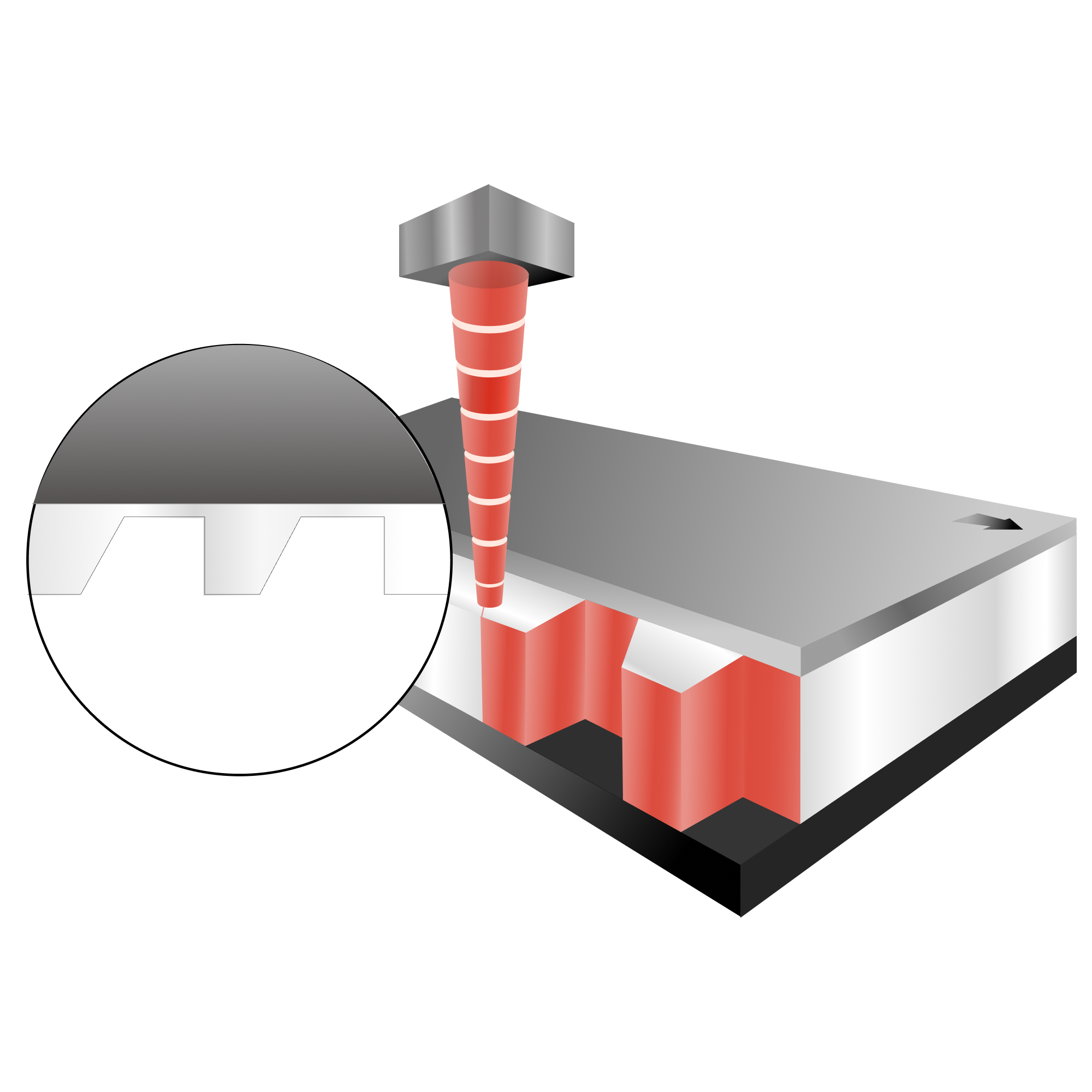
Features
Fast processing speed
Mechanical notching is limited in increasing work speed because the speed between the electrode and cutter must be the same. On the other hand, K2's laser notching with FLY technology can create notches of various shapes without stopping the material. Although it depends on the thickness of the electrode being processed and the design of the notch, the roll-to-roll operation speed can be increased by 20 to 30% compared to conventional mechanical methods. (eg, machine: 1-1.2m/s, laser: 1.5m/s)
CAPEX
Mechanical tools that must be machined very precisely have a very short working life and require periodic polishing and replacement due to wear and tear. Laser processing, on the other hand, does not require replacement of consumable materials, so high CAPEX can be achieved even with low OPEX. Furthermore, the processing shape can be changed at any time, which maximizes the usability of the facility.
Excellent cut quality
The quality of the cut surface determines the longevity of the battery cell. In particular, BURR generated on foil and excessive peeling of coating materials are the main causes of SHORT CIRCUIT. K2's high-speed precision scanner minimizes the HAZ area of laser energy, so unnecessary material deformation and cut surface damage do not occur.
Fast processing speed
Mechanical notching is limited in increasing work speed because the speed between the electrode and cutter must be the same. On the other hand, K2's laser notching with FLY technology can create notches of various shapes without stopping the material. Although it depends on the thickness of the electrode being processed and the design of the notch, the roll-to-roll operation speed can be increased by 20 to 30% compared to conventional mechanical methods. (eg, machine: 1-1.2m/s, laser: 1.5m/s)
CAPEX
Mechanical tools that must be machined very precisely have a very short working life and require periodic polishing and replacement due to wear and tear. Laser processing, on the other hand, does not require replacement of consumable materials, so high CAPEX can be achieved even with low OPEX. Furthermore, the processing shape can be changed at any time, which maximizes the usability of the facility.
Excellent cut quality
The quality of the cut surface determines the longevity of the battery cell. In particular, BURR generated on foil and excessive peeling of coating materials are the main causes of SHORT CIRCUIT. K2's high-speed precision scanner minimizes the HAZ area of laser energy, so unnecessary material deformation and cut surface damage do not occur.
Free
High
High
minimum
Core Technology
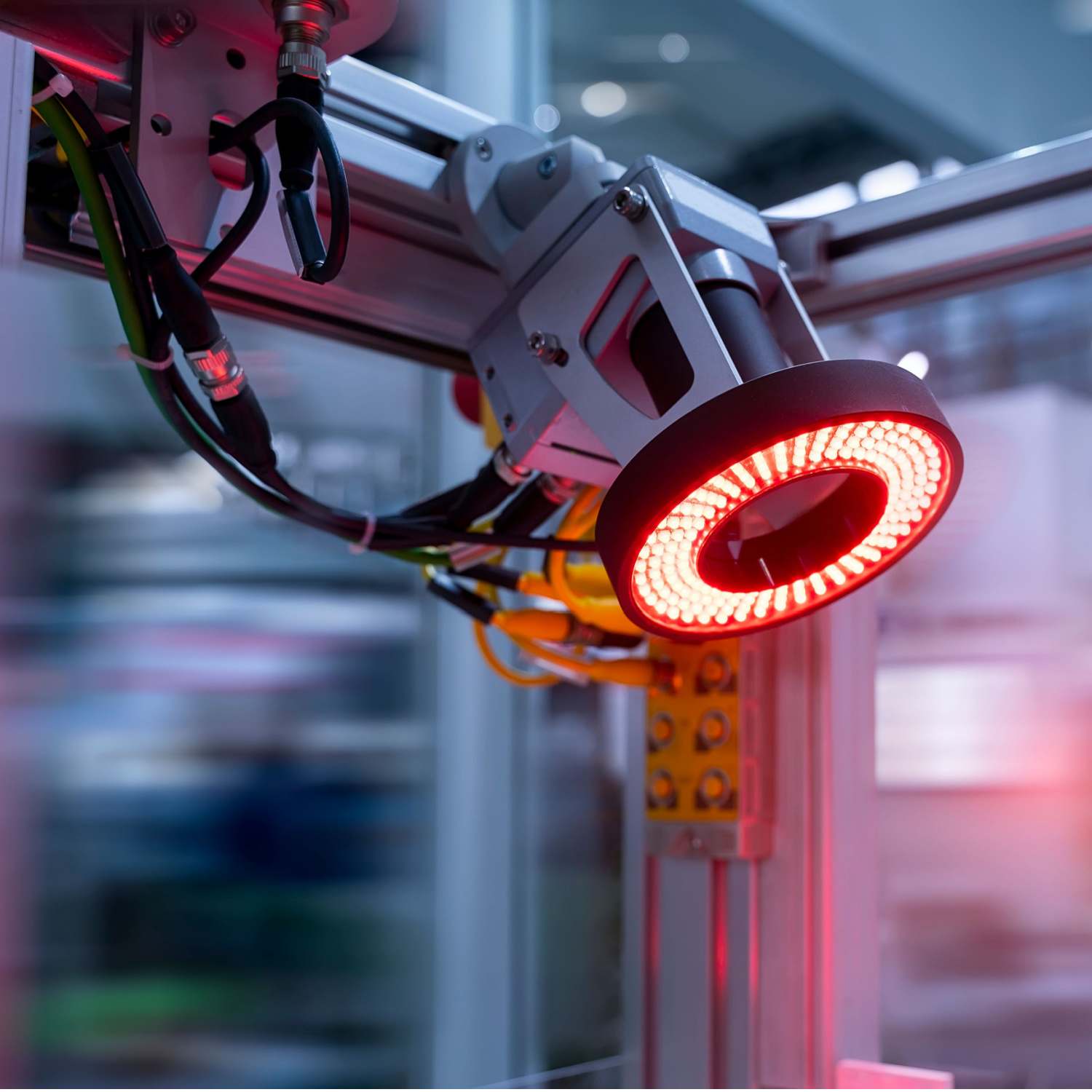
LINE ORGANCE
The vision camera calculates the line and angle on both sides of the ELECTRODE entering as the roll unrolls. Unlike physical cutting, laser notching finds a new cutting line in REAL TIME without changing the position of the device or stopping the facility, even if the material is wrong. This is because a high-speed scanner can move the laser beam as quickly as the compensation position recognized by the vision.
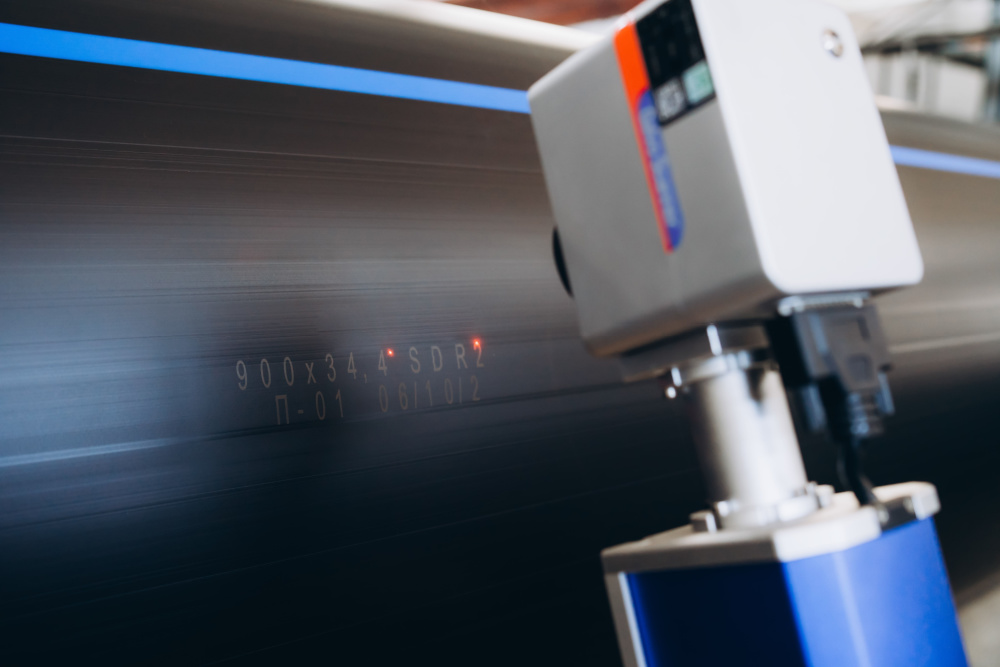
FLY CUTTING
Since mechanical notching involves physical contact between the cutting edge and the material, processing must be performed while the roll is stopped to prevent creasing and frictional heat of the electrode. Also, DOWNTIME is bound to occur every time the design of ELECTRODE is changed or the cutting edge is replaced periodically. Laser notching can process complex NOTCH designs even when the roll is moving at high speed.
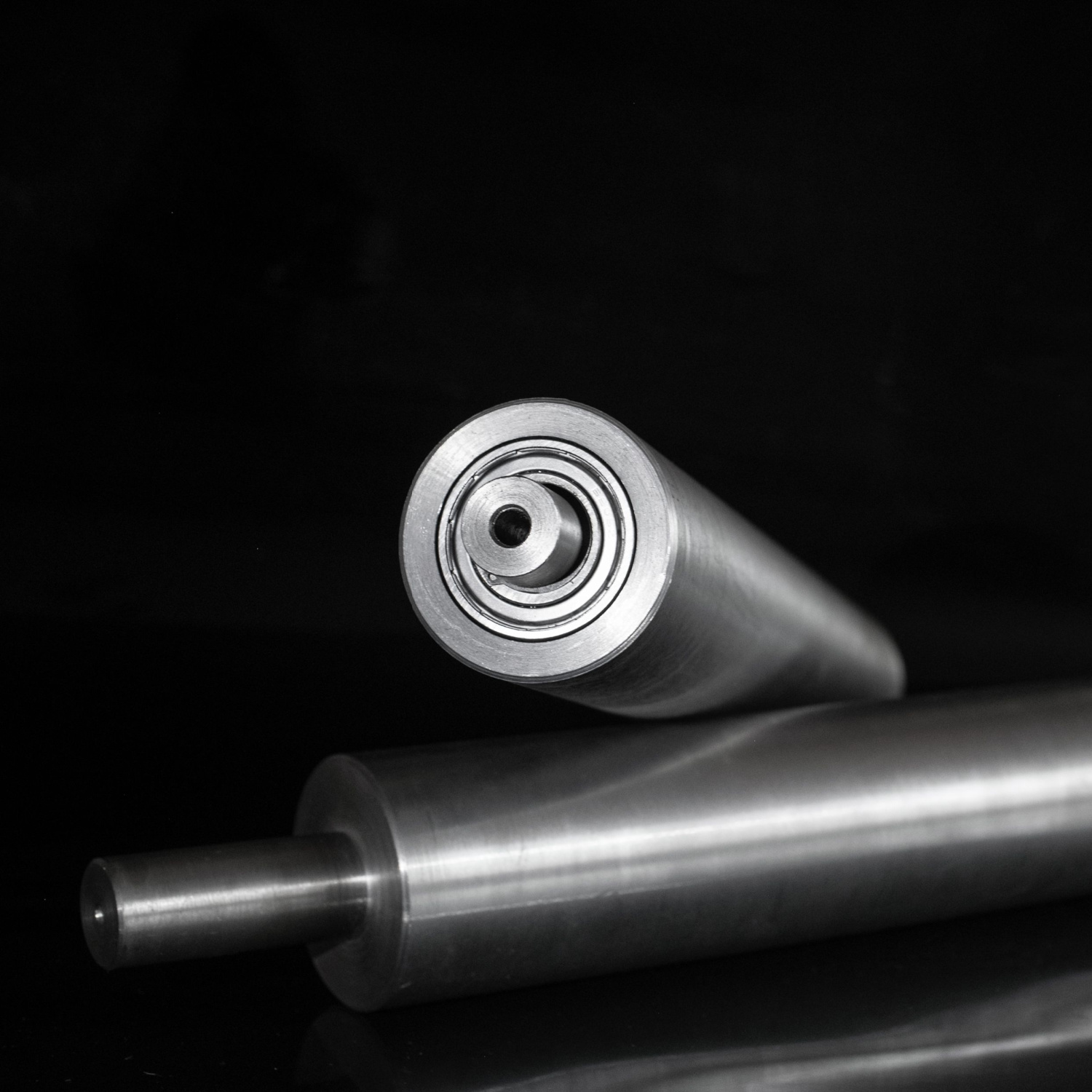
Slope control
When performing roll-to-roll, the most important thing is to prevent warping and creasing by maintaining constant tension and direction. In particular, laser notching requires a constant transfer rate of the roll because the focused beam moves at a high speed. K2's notching machine is equipped with various detectors so that electrode winding and position search, electrode cutting, and by-product removal can be carried out quickly to perform electrode winding and perform complete trajectory control.
Core Technology
Heading
Lorem ipsum dolor sit amet, consectetur adipiscing elit. Suspendisse varius enim in eros elementum tristique. Duis cursus, mi quis viverra ornare, eros dolor interdum nulla, ut commodo diam libero vitae erat. Aenean faucibus nibh et justo cursus id rutrum lorem imperdiet. Nunc ut sem vitae risus tristique posuere.
Heading
Lorem ipsum dolor sit amet, consectetur adipiscing elit. Suspendisse varius enim in eros elementum tristique. Duis cursus, mi quis viverra ornare, eros dolor interdum nulla, ut commodo diam libero vitae erat. Aenean faucibus nibh et justo cursus id rutrum lorem imperdiet. Nunc ut sem vitae risus tristique posuere.
Heading
Lorem ipsum dolor sit amet, consectetur adipiscing elit. Suspendisse varius enim in eros elementum tristique. Duis cursus, mi quis viverra ornare, eros dolor interdum nulla, ut commodo diam libero vitae erat. Aenean faucibus nibh et justo cursus id rutrum lorem imperdiet. Nunc ut sem vitae risus tristique posuere.
Heading
Lorem ipsum dolor sit amet, consectetur adipiscing elit. Suspendisse varius enim in eros elementum tristique. Duis cursus, mi quis viverra ornare, eros dolor interdum nulla, ut commodo diam libero vitae erat. Aenean faucibus nibh et justo cursus id rutrum lorem imperdiet. Nunc ut sem vitae risus tristique posuere.