Pack module welding
Visual inspection of welds and image matching inspections have limitations in determining process defects. An electrical ohmmeter can also be used as a non-destructive test, but the measurement takes a long time and the high voltage in the battery pack also damages the device. K2 implements proactive quality control by applying SEAM TRACKING and OCT to measure melt depth at the same time as laser welding.
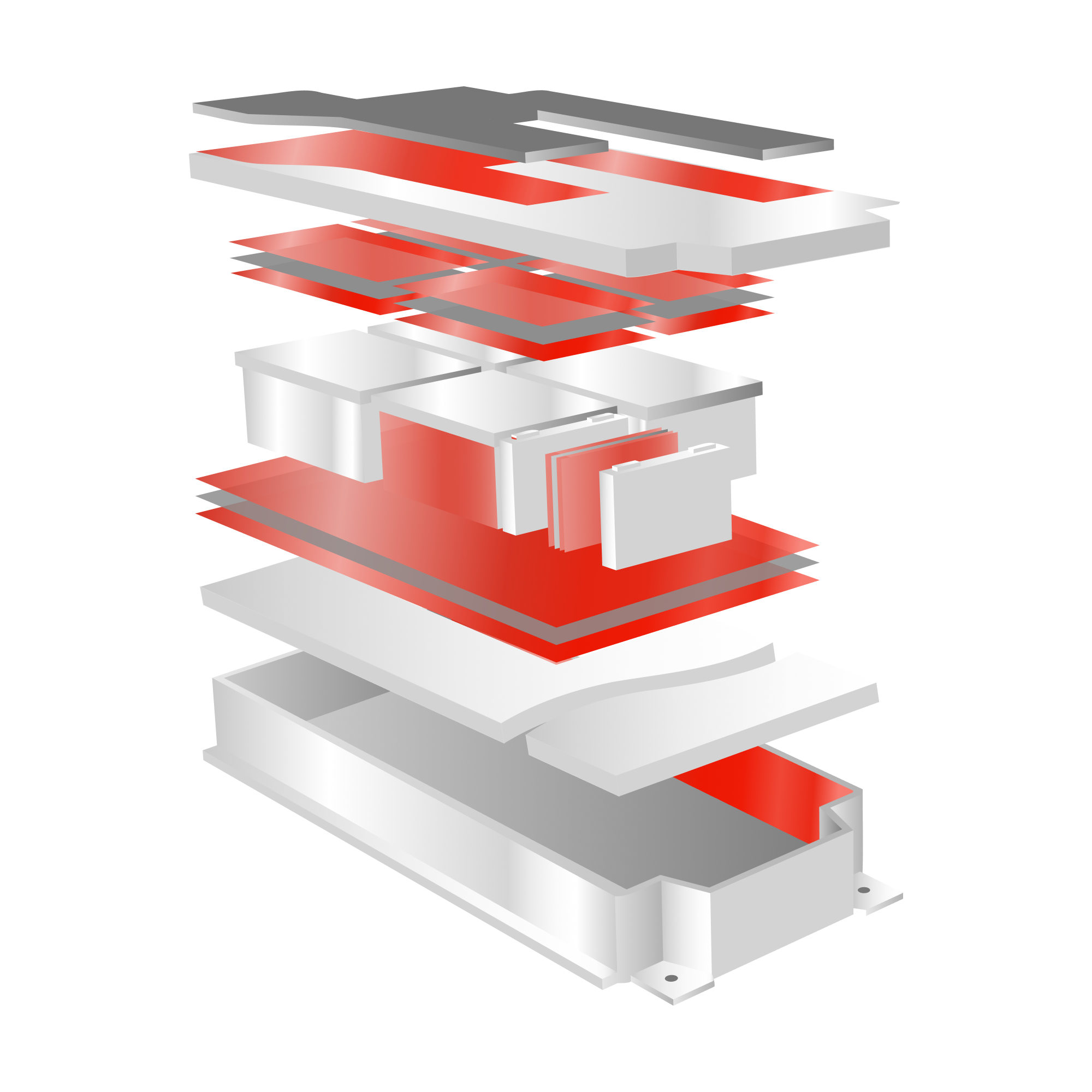
Features
SEAM FINDING
Although the product dimensions are the same, processing tolerances and logistics errors cannot be completely eliminated from the production line. Since laser welding uses a focused beam in a very small size, it is important to properly recognize the position to be processed. K2's JIG & FIXTURE SYSTEM realizes accurate processing by correctly adjusting material positions and navigating SEAM one more time with vision.
LINE TRACKING
Even if the material is properly positioned, welding cannot be performed properly if the joint is not straight or dirty. After SEAM FINDING, LINE TRACKING will confirm with vision whether there are any abnormalities in the path where the laser energy will actually be input. Since the laser system performs camera sensing and laser beam emission through the same optical path, processing can be performed accurately at the searched location.
JOINT Melting
Compared to mechanical bonding such as tightening, bending, and contraction, or chemical bonding using adhesives, welding melts two materials into one, and is suitable for module and pack processes that require high standards of stability and weight. Among them, lasers can flexibly handle various welds compared to other methods such as ELECTRICAL, CHEMICAL, and MECHANICAL (eg. TAILORED BLANK
SEAM FINDING
Although the product dimensions are the same, processing tolerances and logistics errors cannot be completely eliminated from the production line. Since laser welding uses a focused beam in a very small size, it is important to properly recognize the position to be processed. K2's JIG & FIXTURE SYSTEM realizes accurate processing by correctly adjusting material positions and navigating SEAM one more time with vision.
LINE TRACKING
Even if the material is properly positioned, welding cannot be performed properly if the joint is not straight or dirty. After SEAM FINDING, LINE TRACKING will confirm with vision whether there are any abnormalities in the path where the laser energy will actually be input. Since the laser system performs camera sensing and laser beam emission through the same optical path, processing can be performed accurately at the searched location.
JOINT Melting
Compared to mechanical bonding such as tightening, bending, and contraction, or chemical bonding using adhesives, welding melts two materials into one, and is suitable for module and pack processes that require high standards of stability and weight. Among them, lasers can flexibly handle various welds compared to other methods such as ELECTRICAL, CHEMICAL, and MECHANICAL (eg. TAILORED BLANK
POST INSPECTION
When quality inspections are performed by humans, standards vary depending on the operator's experience and proficiency, and erroneous judgments can be made. K2 uses vision and sensors to detect weld bead defects. It detects factors that fall short of standards, from defects such as porosity, spatter, slag, and burns to the height, width, and volume of welds.
Core Technology
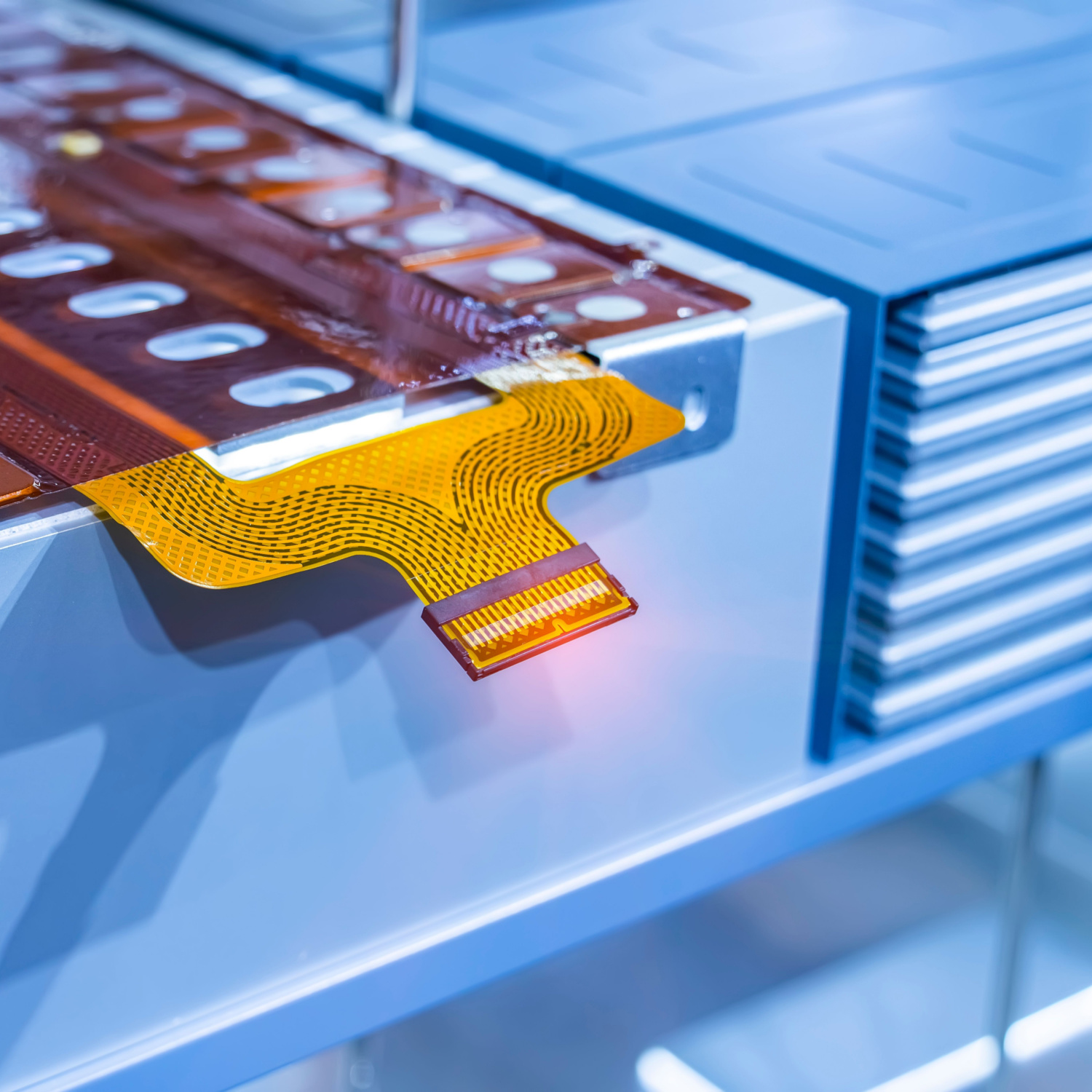
Process technology
It is clear that high-power lasers play a very effective role in performing high-quality welds. However, excessive energy causes material loss due to vaporization, and poor melting weakens bonding strength. K2 has accumulated laser process development technology for many years. We will design a highly complete process with optimal resources.
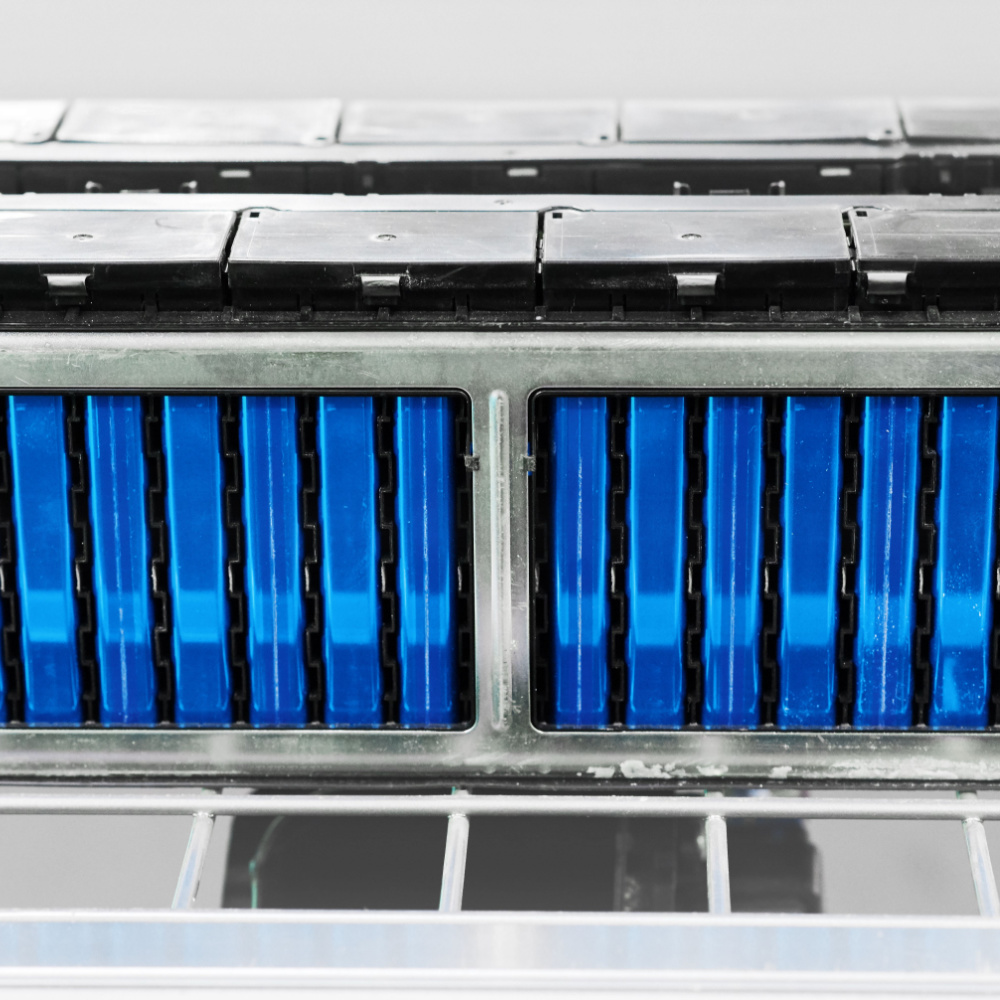
Dissimilar welding
Various heterogeneous materials are used for modules and packs that require combining multiple cells in the form of modules. Since the energy absorption rate and reactivity of individual materials are all different, welding is difficult, and weak welding can easily occur at the joint when sufficient energy is not transferred. Conversely, if the energy is excessive, residual stress can damage the bonded cell. K2's process research team has verified stability by performing welding between various materials.
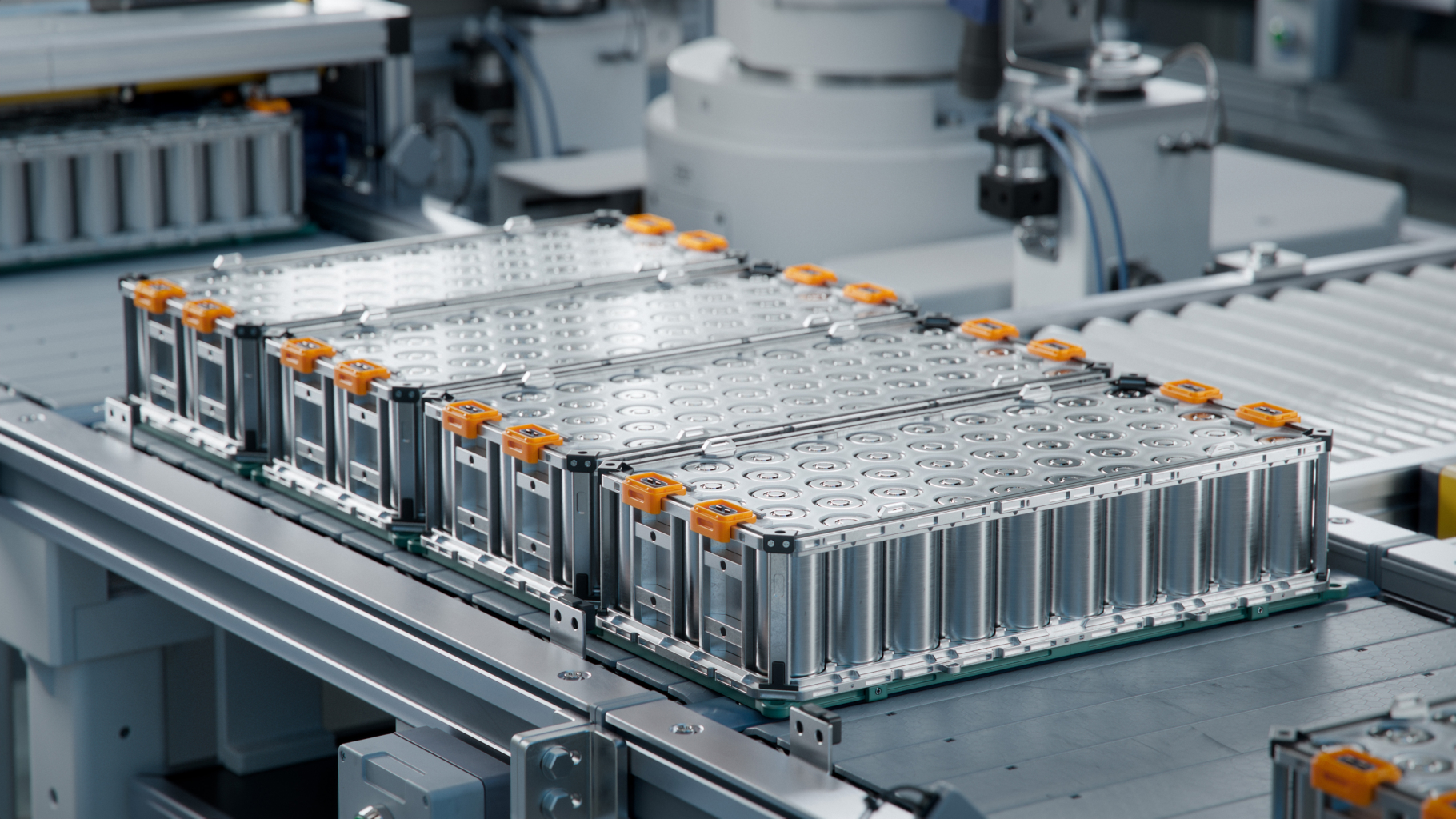
JIG & FIXTURE SYSTEM
Vibrations generated during the process and mechanical contact can damage the inside of the battery cell. Laser systems can reduce potential risk factors through non-contact processing. Furthermore, the JIG & FIXTURE SYSTEM optimized for the customer's module pack prevents deformation of the processing position and material damage due to external influences.
Core Technology
Heading
Lorem ipsum dolor sit amet, consectetur adipiscing elit. Suspendisse varius enim in eros elementum tristique. Duis cursus, mi quis viverra ornare, eros dolor interdum nulla, ut commodo diam libero vitae erat. Aenean faucibus nibh et justo cursus id rutrum lorem imperdiet. Nunc ut sem vitae risus tristique posuere.
Heading
Lorem ipsum dolor sit amet, consectetur adipiscing elit. Suspendisse varius enim in eros elementum tristique. Duis cursus, mi quis viverra ornare, eros dolor interdum nulla, ut commodo diam libero vitae erat. Aenean faucibus nibh et justo cursus id rutrum lorem imperdiet. Nunc ut sem vitae risus tristique posuere.
Heading
Lorem ipsum dolor sit amet, consectetur adipiscing elit. Suspendisse varius enim in eros elementum tristique. Duis cursus, mi quis viverra ornare, eros dolor interdum nulla, ut commodo diam libero vitae erat. Aenean faucibus nibh et justo cursus id rutrum lorem imperdiet. Nunc ut sem vitae risus tristique posuere.
Heading
Lorem ipsum dolor sit amet, consectetur adipiscing elit. Suspendisse varius enim in eros elementum tristique. Duis cursus, mi quis viverra ornare, eros dolor interdum nulla, ut commodo diam libero vitae erat. Aenean faucibus nibh et justo cursus id rutrum lorem imperdiet. Nunc ut sem vitae risus tristique posuere.