Technical support
We provide technical support services based on SLA (Service Level Agreement) levels to maintain stable facility operation and manufacturing quality. As a laser specialist company that has supplied solutions to domestic and international global vendors, K2 is always striving to increase facility availability by quickly solving problems.
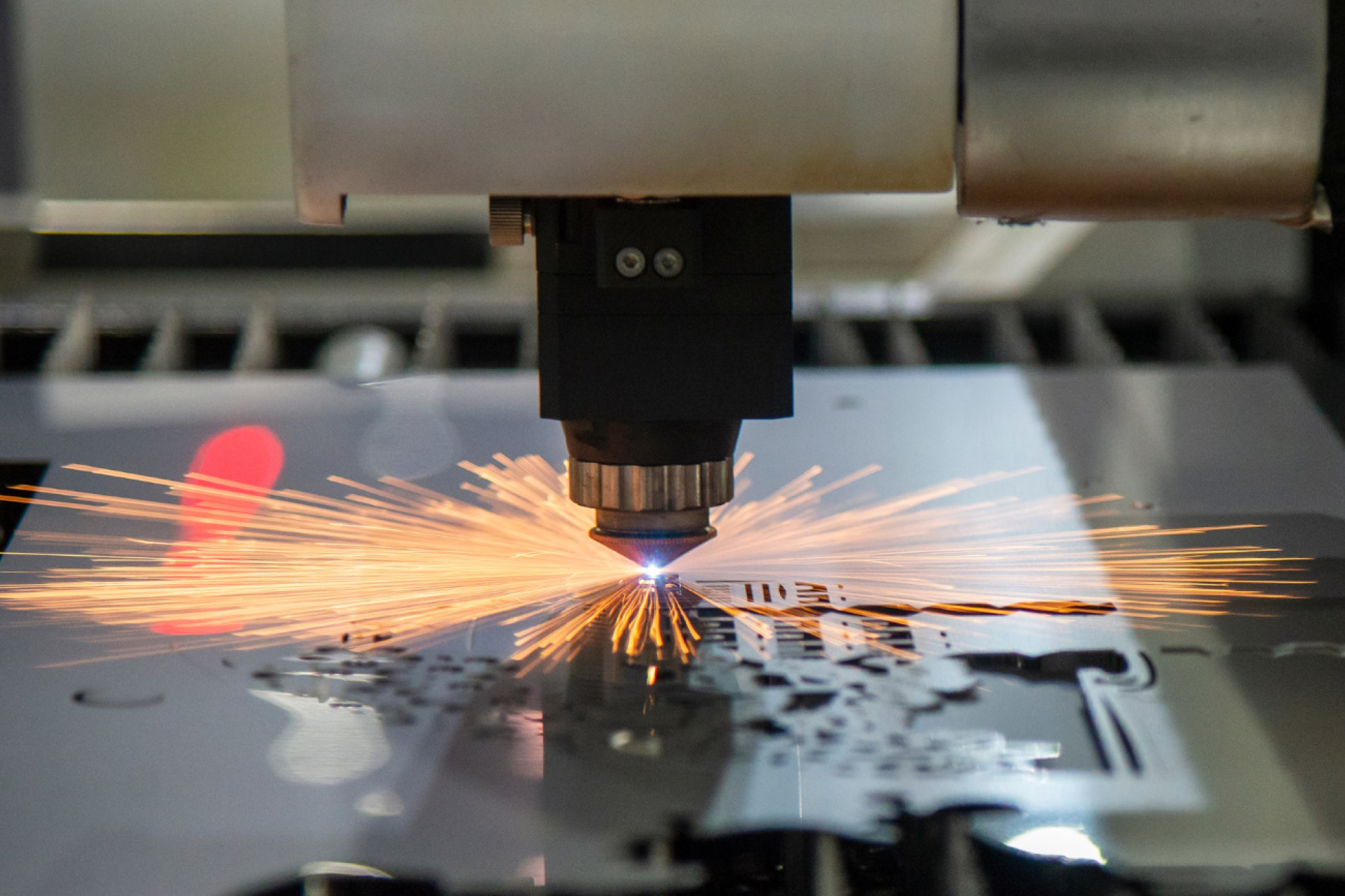
Features
STANDARD CARE
We provide technical support that meets customer standards in line with industry standards. We spare no effort to support the stabilization of operating processes, from securing mass production capacity for domestic and overseas lines to improving process technology.
ACTIVE CARE
We carry out on-site repairs, repairs, inspections, and replacement of consumables in accordance with customer requests. Facility availability can be increased by maintaining optimal equipment operating conditions.
PRO ACTIVE CARE
If ACTIVE CARE is technical support performed in response to customer requests, PRO ACTIVE CARE proactively provides preventative maintenance and training. If the purpose is diverse, such as an experimental and development facility, or the user's level of skill is not high, periodic care is required to perform tasks safely and correctly.
STANDARD CARE
We provide technical support that meets customer standards in line with industry standards. We spare no effort to support the stabilization of operating processes, from securing mass production capacity for domestic and overseas lines to improving process technology.
ACTIVE CARE
We carry out on-site repairs, repairs, inspections, and replacement of consumables in accordance with customer requests. Facility availability can be increased by maintaining optimal equipment operating conditions.
PRO ACTIVE CARE
If ACTIVE CARE is technical support performed in response to customer requests, PRO ACTIVE CARE proactively provides preventative maintenance and training. If the purpose is diverse, such as an experimental and development facility, or the user's level of skill is not high, periodic care is required to perform tasks safely and correctly.
Performance care
We rent lasers so that your business is not affected by poor laser performance or failure. Production can continue while repairs are completed, and replacement and rental costs may be incurred, including some consumables.
Customer Service
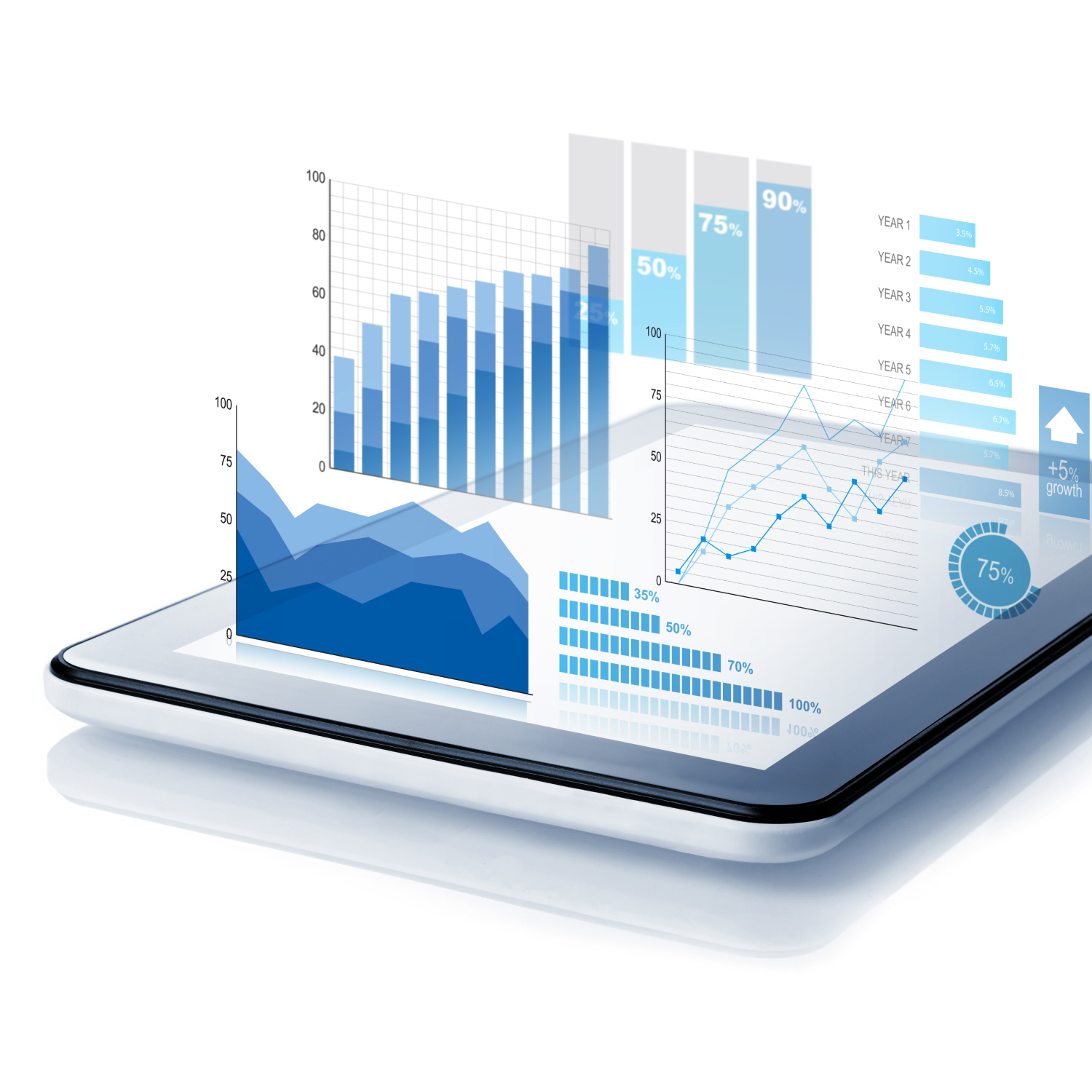
Remote response
In order to deal with customer difficulties as quickly as possible, we communicate with field personnel via remote guidance. Furthermore, for accurate situation diagnosis and cause assessment, appropriate actions and guidance are provided after remote access to the control PC.
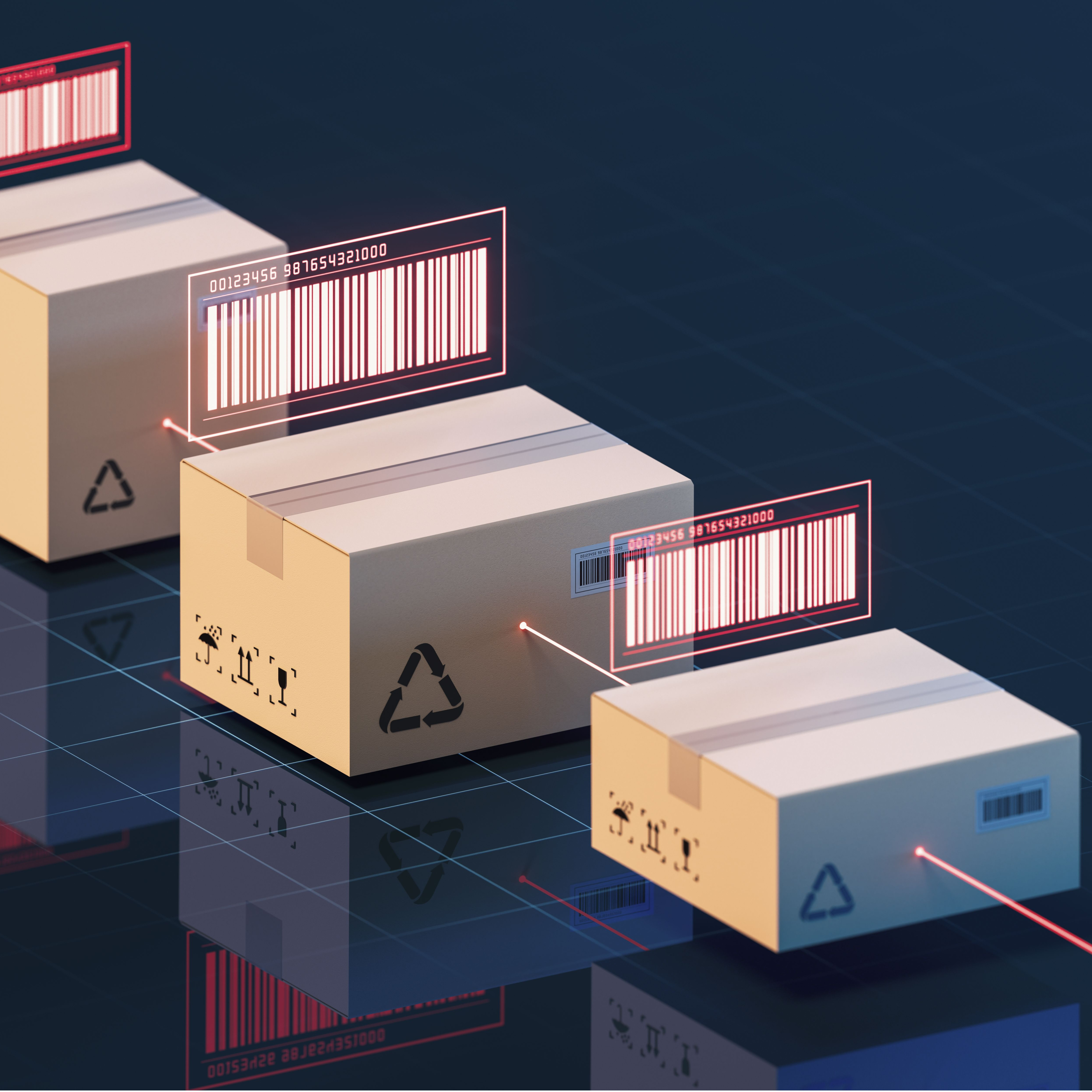
Track management
Appropriate maintenance must be carried out regularly to ensure high productivity. This also includes maintenance of mechanical, electrical, and control parts. To prevent customer difficulties in operation and maintenance, K2 engineers actively track the situation and allocate appropriate resources.
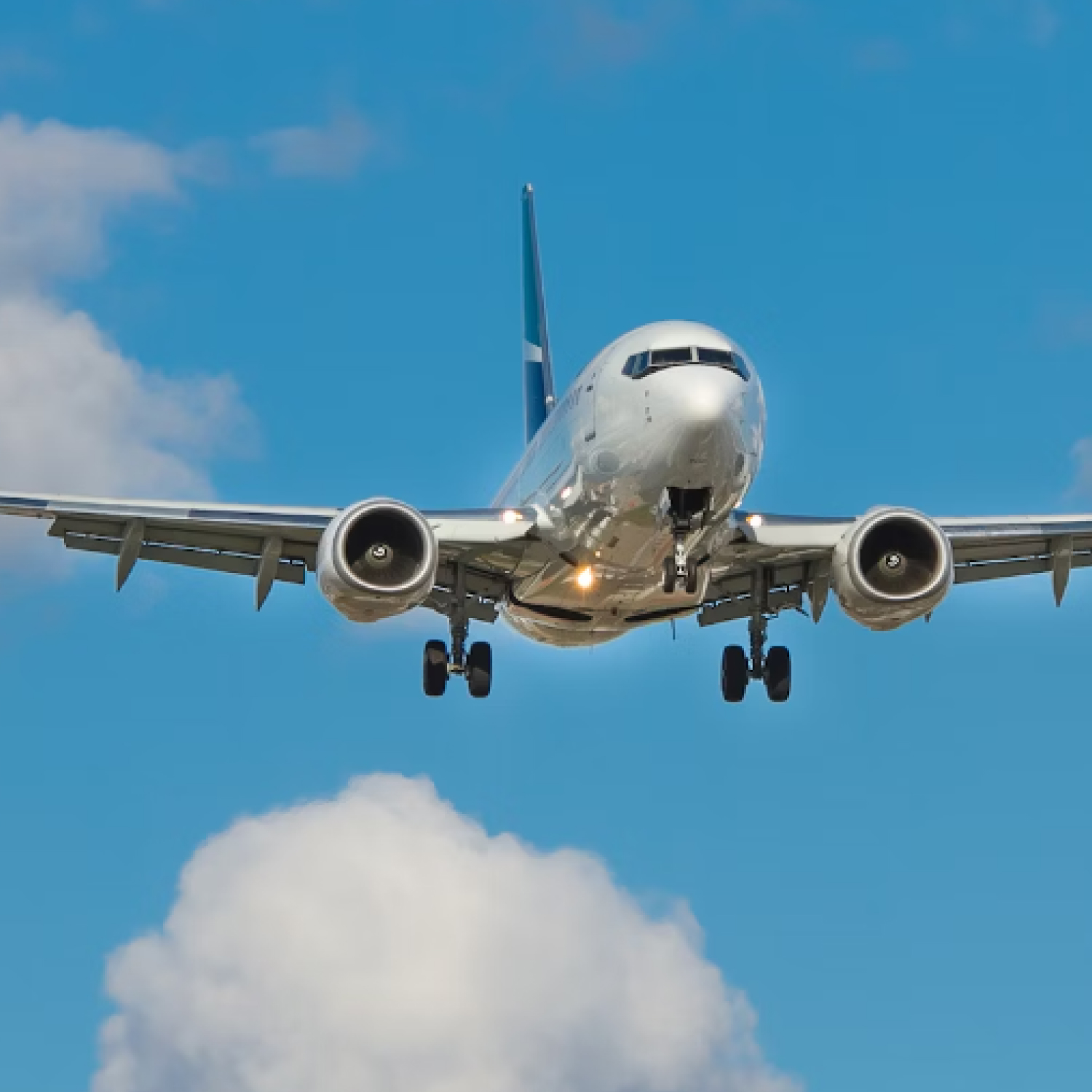
Site visits
K2, which supplies equipment to global production sites, dispatches engineers to facility operation points to provide inspection, diagnosis, replacement, and modification services. A professional team of qualified and experienced service engineers is quickly deployed on-site within reasonable limits.
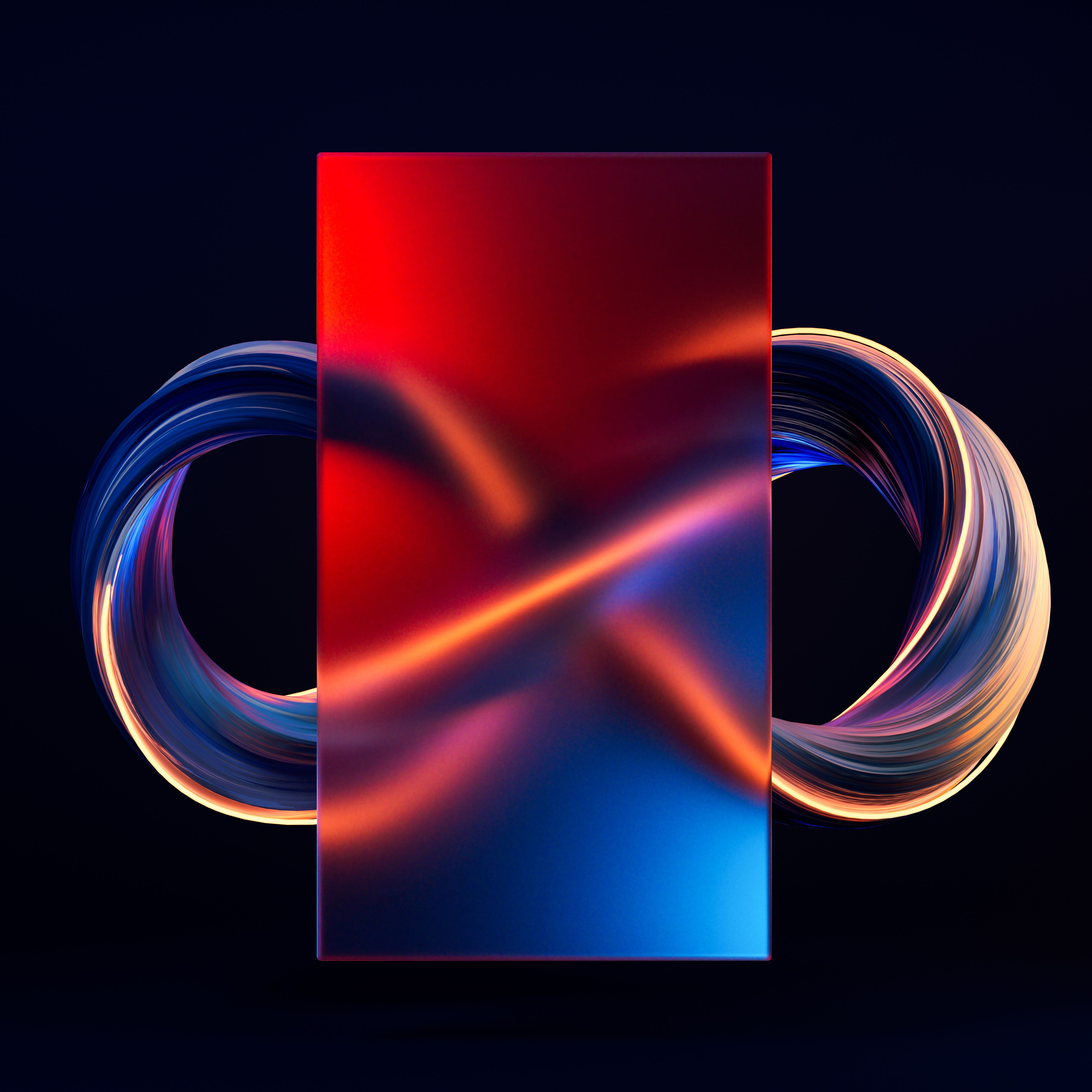
Dedicated service
K2, which has been trusted by customers for a long time, has professional engineers who have shared that history. Since we have felt the difficulties of our customers firsthand in the field, we promise to support them more enthusiastically than anyone else.