Electrode tab welding
A battery tab is a positive and negative connector that transfers the cell's current to the outside. Since the cell tab is connected to the module bus bar and the module consists of a pack, lasers are an optimal solution for performing thousands of welds from individual cells to the final terminal.
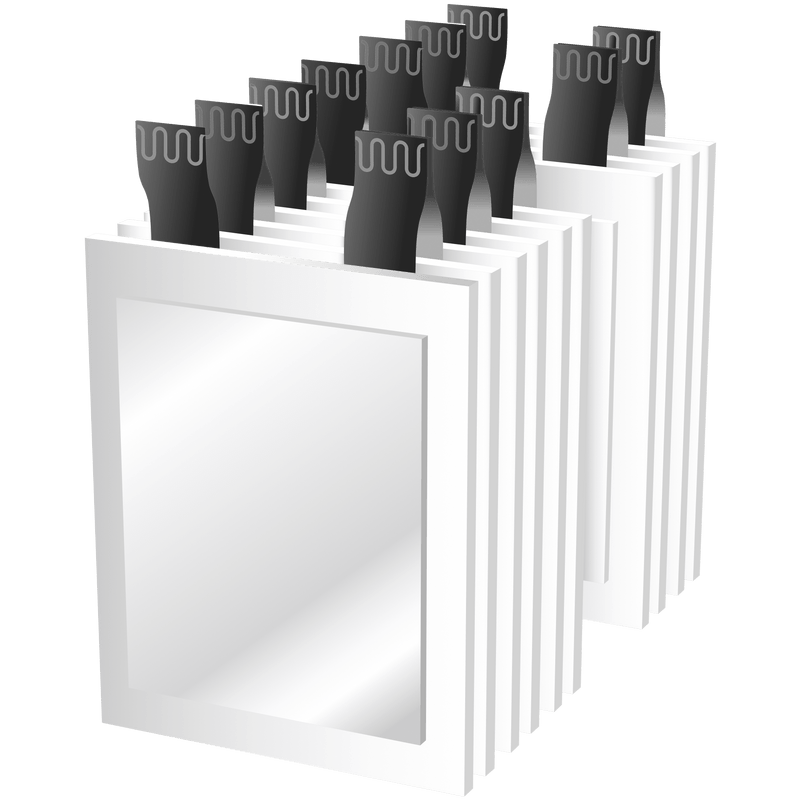
Features
Pre-welding
The metal foil stacks are crimped together before connecting the Current Collector. Ultrasonic compression is common, but lasers can be used for more flexible and faster processing.
Tab welding
Also known as post-welding, leads are attached to the positive and negative electrode tabs of a Stack Cell collector that has been laminated between the foils by pre-welding. Lasers can increase weld strength compared to ultrasonic waves, and real-time in-line monitoring with vision is possible.
Vision Inspection
The lithium-ion polymer battery is sealed, and the terminal and pouch-type outer material are insulated. The lead tap is a key component that transmits current, and the placement position, angle, and size are measured with a coaxial vision system before welding is performed.
Pre-welding
The metal foil stacks are crimped together before connecting the Current Collector. Ultrasonic compression is common, but lasers can be used for more flexible and faster processing.
Tab welding
Also known as post-welding, leads are attached to the positive and negative electrode tabs of a Stack Cell collector that has been laminated between the foils by pre-welding. Lasers can increase weld strength compared to ultrasonic waves, and real-time in-line monitoring with vision is possible.
Vision Inspection
The lithium-ion polymer battery is sealed, and the terminal and pouch-type outer material are insulated. The lead tap is a key component that transmits current, and the placement position, angle, and size are measured with a coaxial vision system before welding is performed.
8-12um
12-20um
60+
Highest
Core Technology
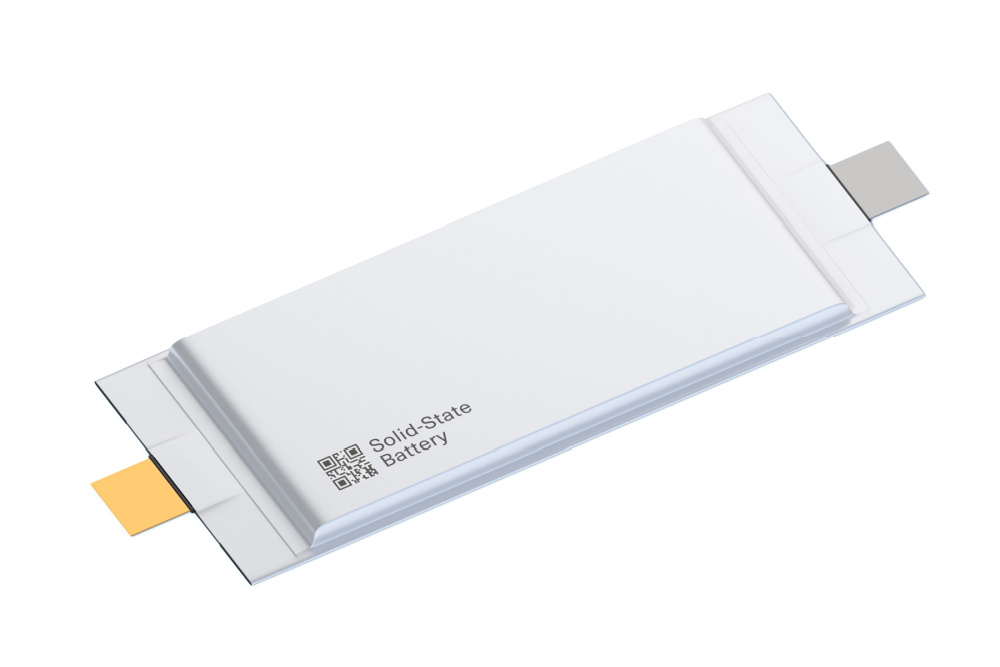
Fine pulse processing
In order to transfer more current, the contact area with the electrode and the thickness of the tap are increasing, and aluminum or copper is being used instead of steel and nickel for the same reason. However, no matter how good the material is, if it is not properly bonded to the cell, energy efficiency will decrease. K2's laser system can maximize the bonding area and density between dissimilar materials by finely processing pulsed beams of several tens of microns in size.
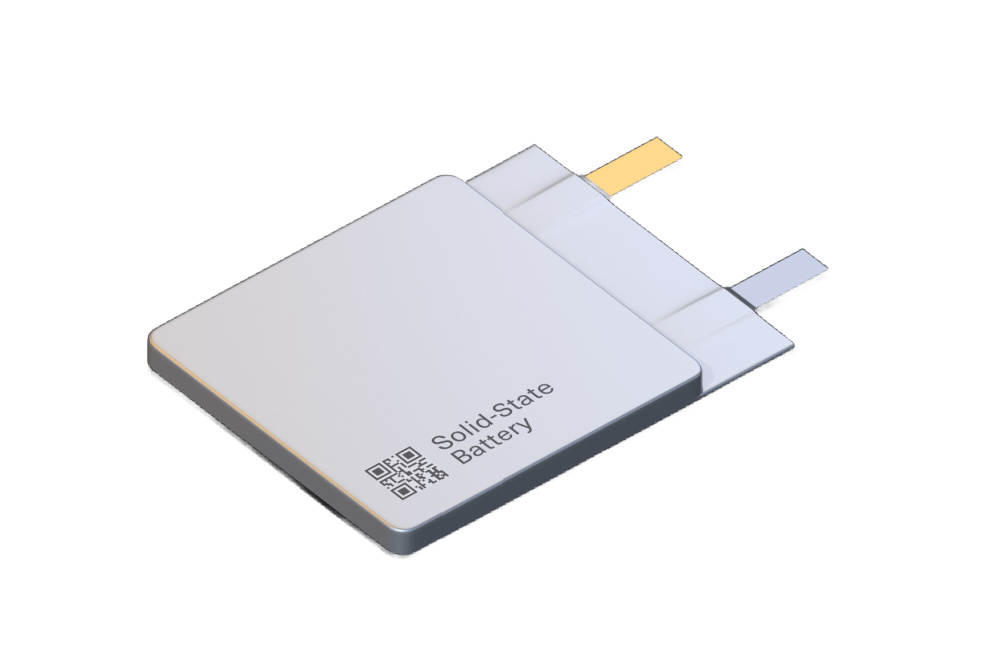
Combined cleaning
Conventional welding processes, such as ultrasound, require separate cleaning to improve electrical contact quality and weld strength. By using a laser, cleaning and welding can be performed all at once, simplifying the process. As the high-precision laser beam is repeatedly irradiated, the contamination is vaporized and the surface warms up, so the speed and quality of welding also improves.
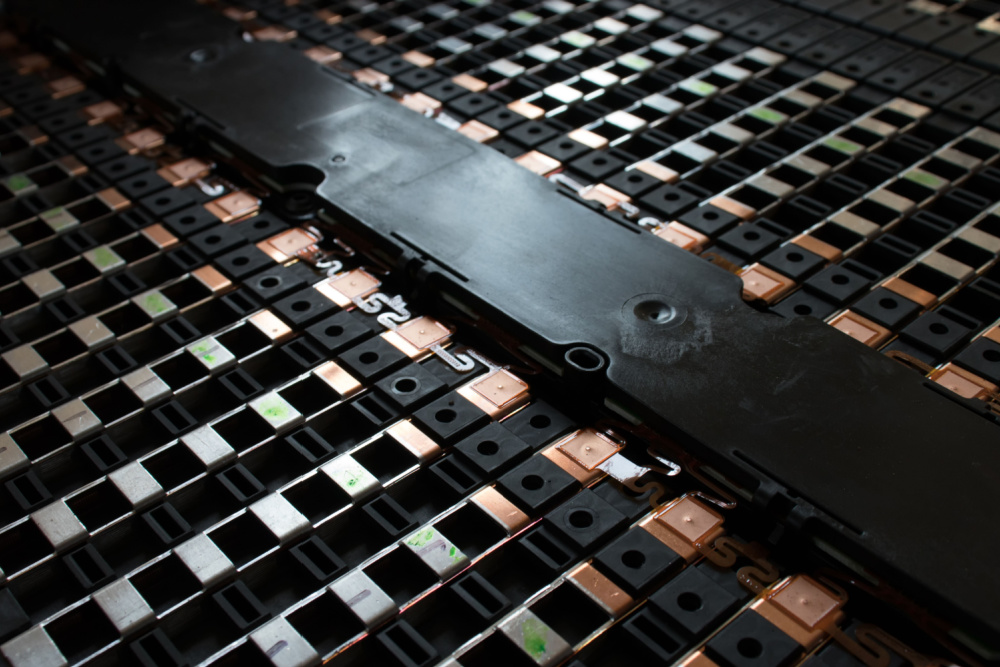
perfect weld
If the welding is wrong, the electrical contact resistance will be high, creating a power loss area. Furthermore, every time an electric current passes through, heat can damage the surrounding area. Although the heat generated by a single tab is small, the overall heat generated by the module and pack can never be overlooked. K2 designs the process to increase the contact area of the joint and improves current distribution and conductivity.
Core Technology
Heading
Lorem ipsum dolor sit amet, consectetur adipiscing elit. Suspendisse varius enim in eros elementum tristique. Duis cursus, mi quis viverra ornare, eros dolor interdum nulla, ut commodo diam libero vitae erat. Aenean faucibus nibh et justo cursus id rutrum lorem imperdiet. Nunc ut sem vitae risus tristique posuere.
Heading
Lorem ipsum dolor sit amet, consectetur adipiscing elit. Suspendisse varius enim in eros elementum tristique. Duis cursus, mi quis viverra ornare, eros dolor interdum nulla, ut commodo diam libero vitae erat. Aenean faucibus nibh et justo cursus id rutrum lorem imperdiet. Nunc ut sem vitae risus tristique posuere.
Heading
Lorem ipsum dolor sit amet, consectetur adipiscing elit. Suspendisse varius enim in eros elementum tristique. Duis cursus, mi quis viverra ornare, eros dolor interdum nulla, ut commodo diam libero vitae erat. Aenean faucibus nibh et justo cursus id rutrum lorem imperdiet. Nunc ut sem vitae risus tristique posuere.
Heading
Lorem ipsum dolor sit amet, consectetur adipiscing elit. Suspendisse varius enim in eros elementum tristique. Duis cursus, mi quis viverra ornare, eros dolor interdum nulla, ut commodo diam libero vitae erat. Aenean faucibus nibh et justo cursus id rutrum lorem imperdiet. Nunc ut sem vitae risus tristique posuere.